Material Handling Automation
Streamline your process with solutions that effectively address all your needs, from corrugators to finished goods.
Corrugators
It all starts at the corrugator. From end to end, our solutions handle materials with precision and care.
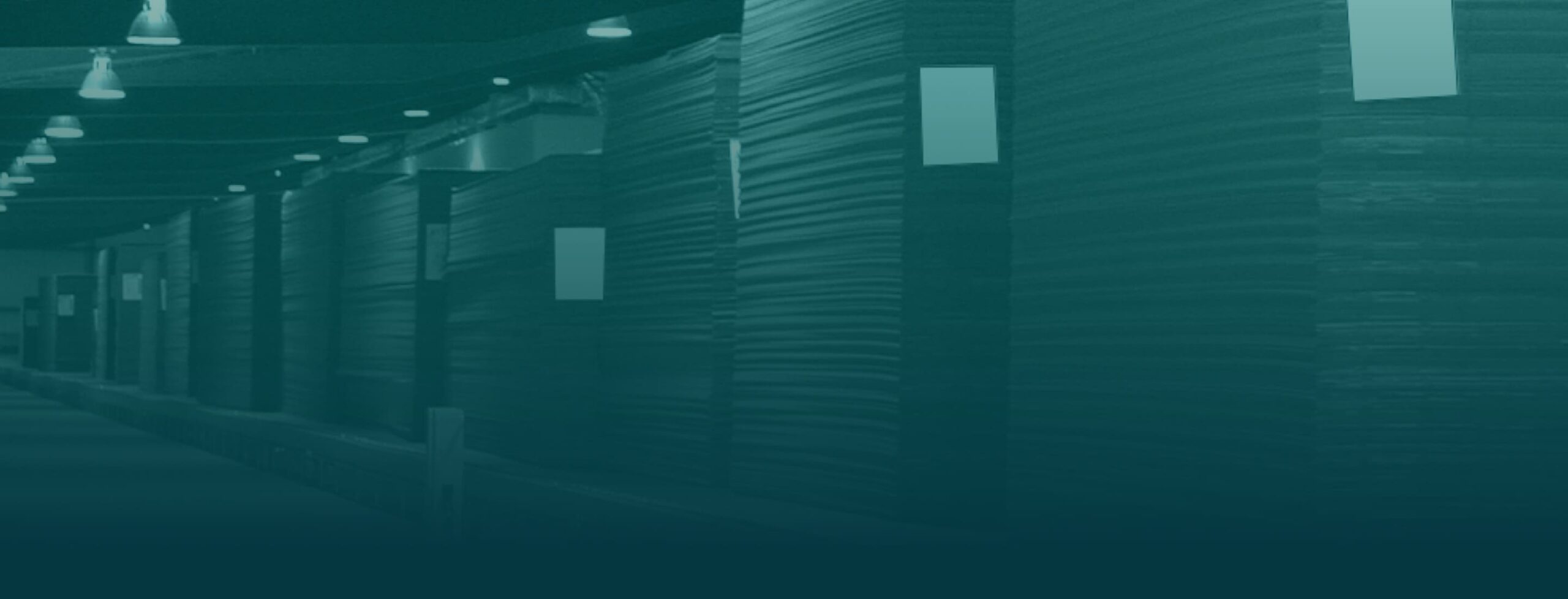
Bundle Line
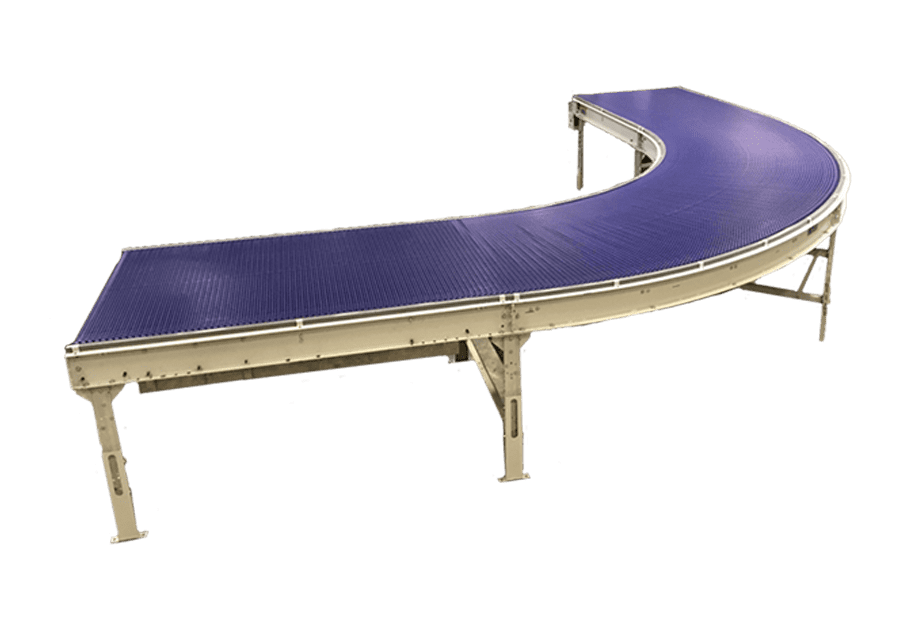
Stable Stack Bundle Conveyor
Systec’s Stable Stack Bundle Conveyor (SSBC) is a material handling solution for when a smooth surface is required. The SSBC Curve has advantages over standard bundle conveyor curves because it eliminates the gap between rollers and product maintains a 90-degree orientation.

AutoStak Robotic Load Former
The AutoStak Robotic Load Former is responsible for transferring bundles of corrugated material from the inbound conveyor system to an Automatan or customer-supplied load former utilizing the End-of-Arm Tool (EOAT) and custom programming. The AutoStak Palletizing EOAT is responsible for transferring the corrugate bundles from the outbound conveyor system to the palletizing area utilizing paddles. The AutoStak conveyor section will justify the bundle to the proper position on the conveyors, move the bundle into the AutoStak robotic bundle feed section, and then assist the robot in transferring the bundle into the Automatan’s or the plant’s load former, in the proper position for each specific layer pattern.
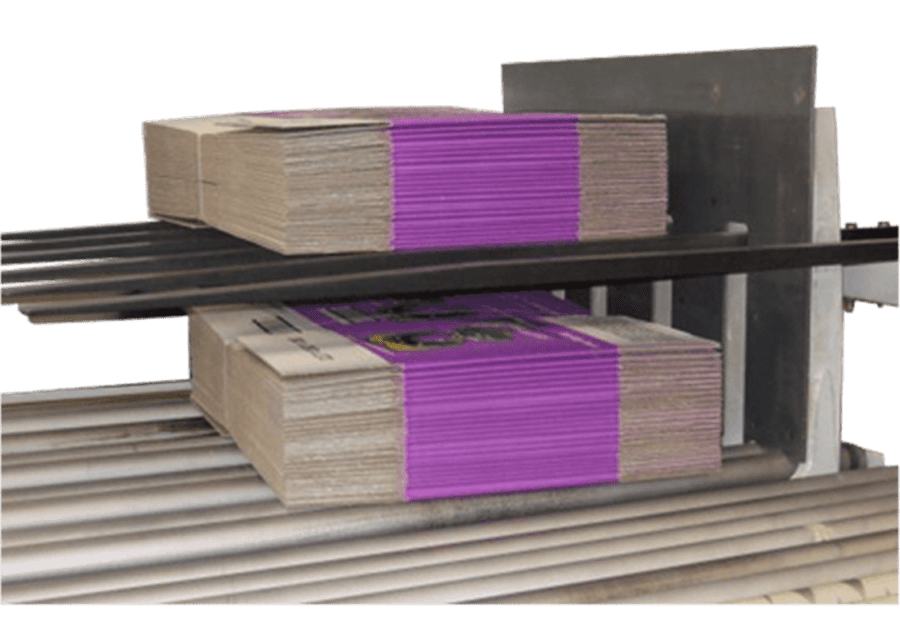
Bundle Doubler
Bundles of cases or diecut sheets, either tied or untied, are conveyed via the entry conveyor to a pop-up blade stop. The first pack enters the bundle doubler and runs to the back stop. The forks lift the bundle to a set height. The bundle doubler is normally supplied with a desktop panel with processor and PLC controls, with an HMI (Human Machine Interface) to allow certain manual operations. The unit is adjustable from 35.5" to 43.3", and can be run in automatic or manual mode from an HMI station.
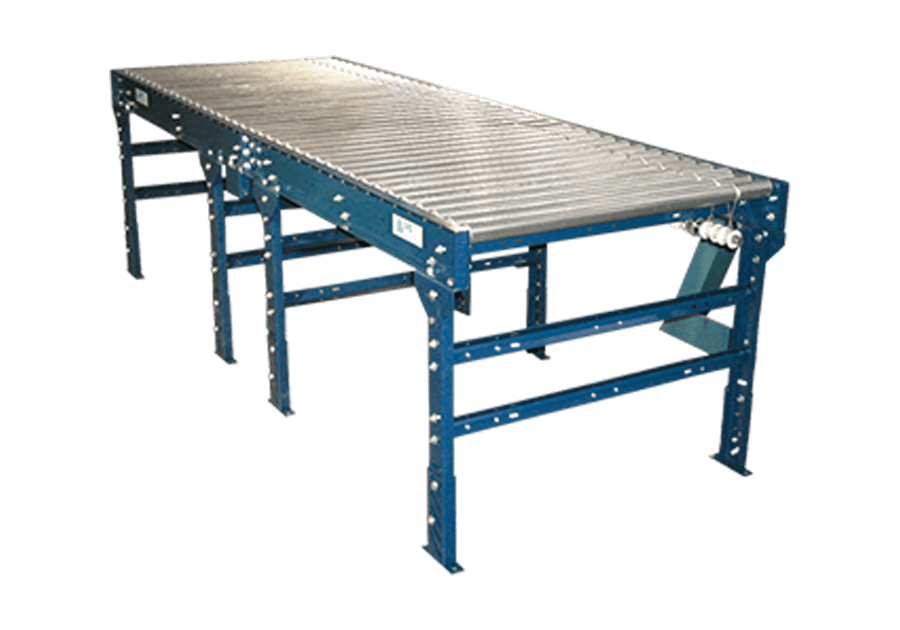
Performance Line Shaft Conveyor
Systec’s Performance Line Shaft Conveyor (PLSC) is engineered for small bundle handling and load accumulation. All PLSCs come with adjustable leg stands to set the working height for comfortable, ergonomic conditions. This also allows the conveyor to be set at the required height at the feed end of the conveyor. Height differences between the beginning and ending of the conveyor line can be adjusted throughout the length of the line. This is a very low-maintenance device applying the most advanced safety designs and features. The PSLC is a line-shaft-driven roller conveyor. The rollers are driven using friction drive spools on the drive shaft. Loads can be stopped with a physical barrier, or with pneumatic brakes. The PLSC offers optional devices for load transfer onto or off the conveyor line, such as a Belt Transfer Device (BTD).
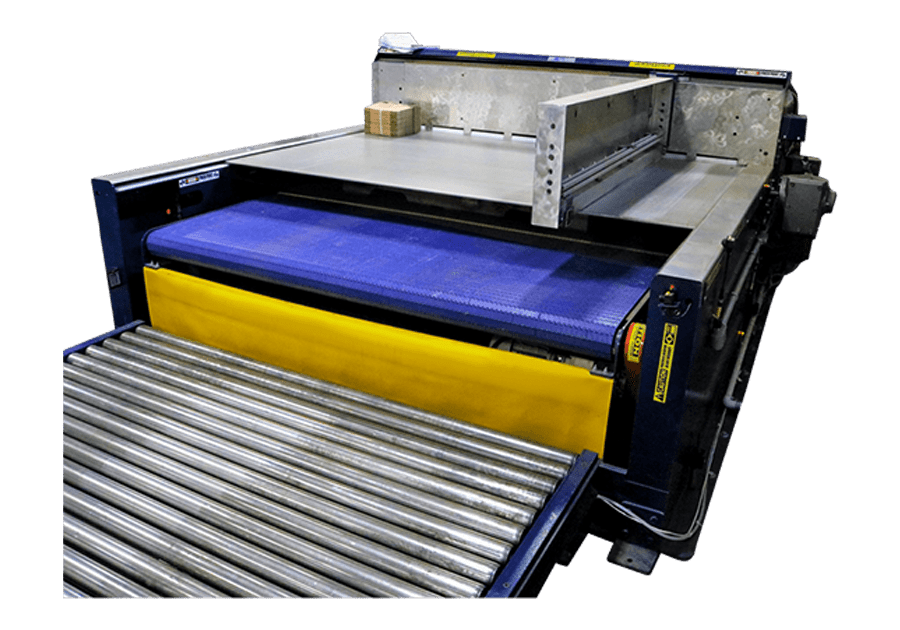
Unit Load Former
Systec Conveyors Generation III Unit Load Former (GEN III) is a fully electric load former. Its standards—such as a plastic bed on the lift, polished stainless steel high-use areas, and powered backstop—make it the most cost-effective load former in the market.
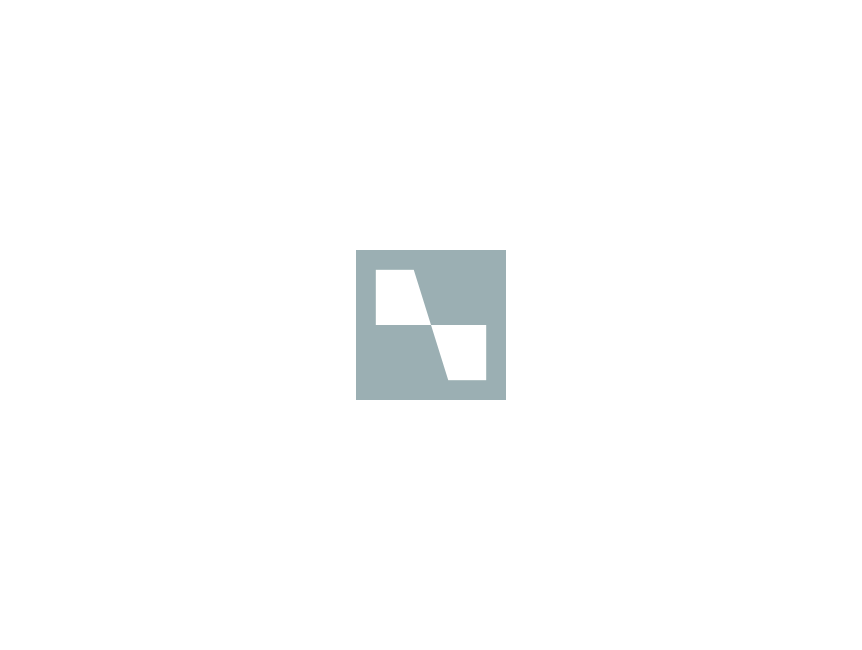
Performance Line Passive Right-Angle Transfer
Systec’s Performance Line Passive Right Angle Transfer, or PLRAT, is designed to allow for instantaneous transitions of loads, all while maintaining orientation. It is an alternative to belt transfers and allows for more flexibility and load building capabilities, all while maintaining a smaller footprint than a traditional 90-degree curve. Because this device uses a nonactivated roller belt, it has fewer moving parts and maintenance points than the competition. The conveyor can be equipped with casters and quick-disconnect plugs to allow access into the area. Speeds can be controlled through the variable frequency drive.
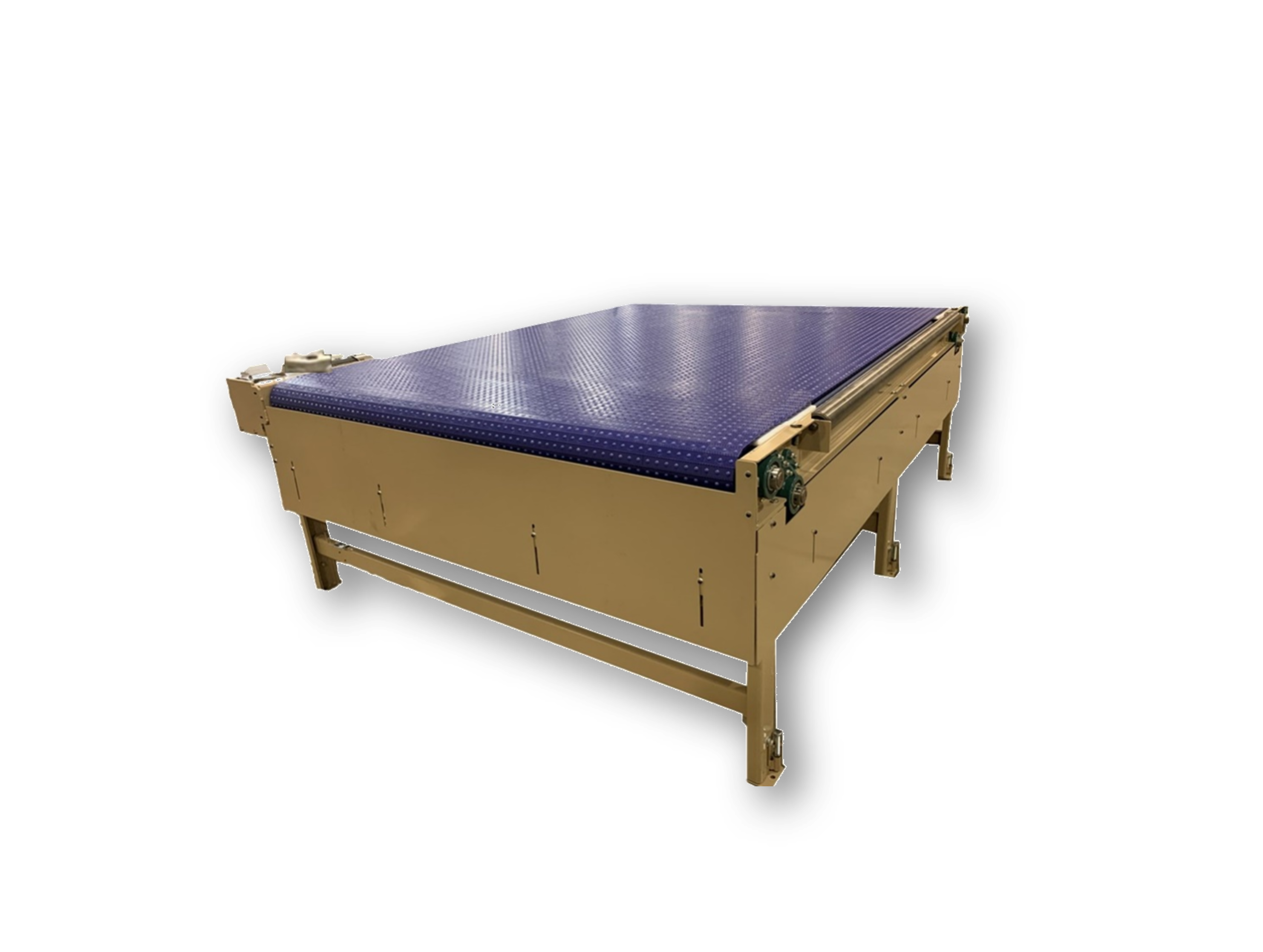
Active Ball Bundle Right-Angle-Transfer
Systec’s Active Ball Belt Right-Angle Transfer (ABBRAT) utilizes the latest technology of Active Ball belt to enable immediate right-angle load transfers in a fraction of time of other devices. Systec’s Active Ball Device family provides a very effective method of rapid and precise load right angle transfer right-angle or pass-through directions. Unlike the Passive Right-Angle-Transfer device, the ABBRAT can discharge loads in multi-directional modes, as well as load-build prior to discharge.
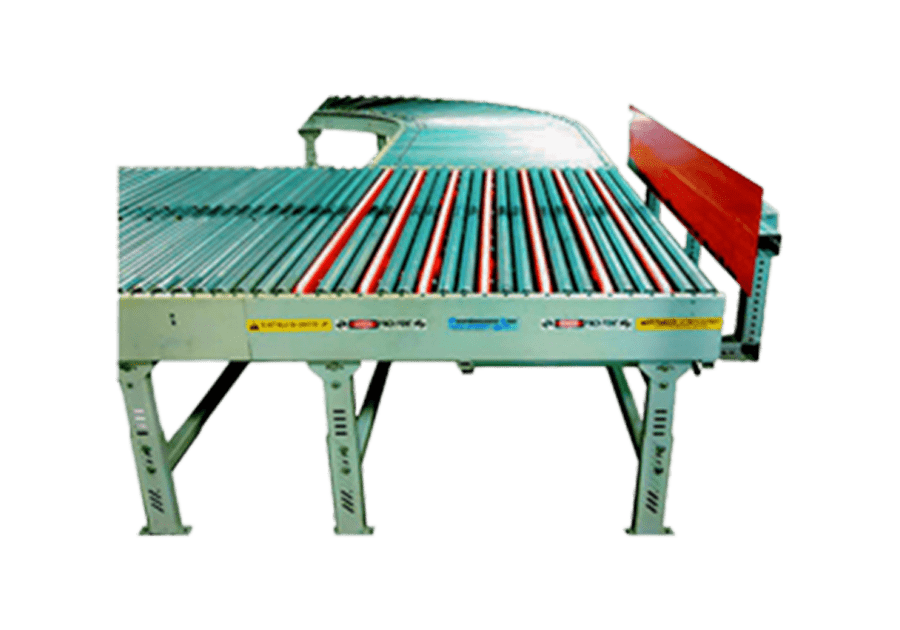
Performance Line Bundle Transfer Ejector
Systec’s Performance Line Bundle Transfer Ejector, or PBTE, is unique in that it can integrate with vision inspection systems to allow for the quarantine ejection of defective loads, as well as a bundle transfer for normal product flow. Systec’s PBTE integrates with zoned Performance Line Bundle Conveyor for the best control. The device is ideal for use at a corner, allowing for maximum surge and straight cornering where registration is not an issue when building a load. This is a very-low maintenance device applying the most advanced safety designs and features. Based on the application, through optional load controls, loads can enter or exit, or within certain applications, the device can act as a one-, two-, three- or four-way intersection.
Flexo Infeed/Outfeed
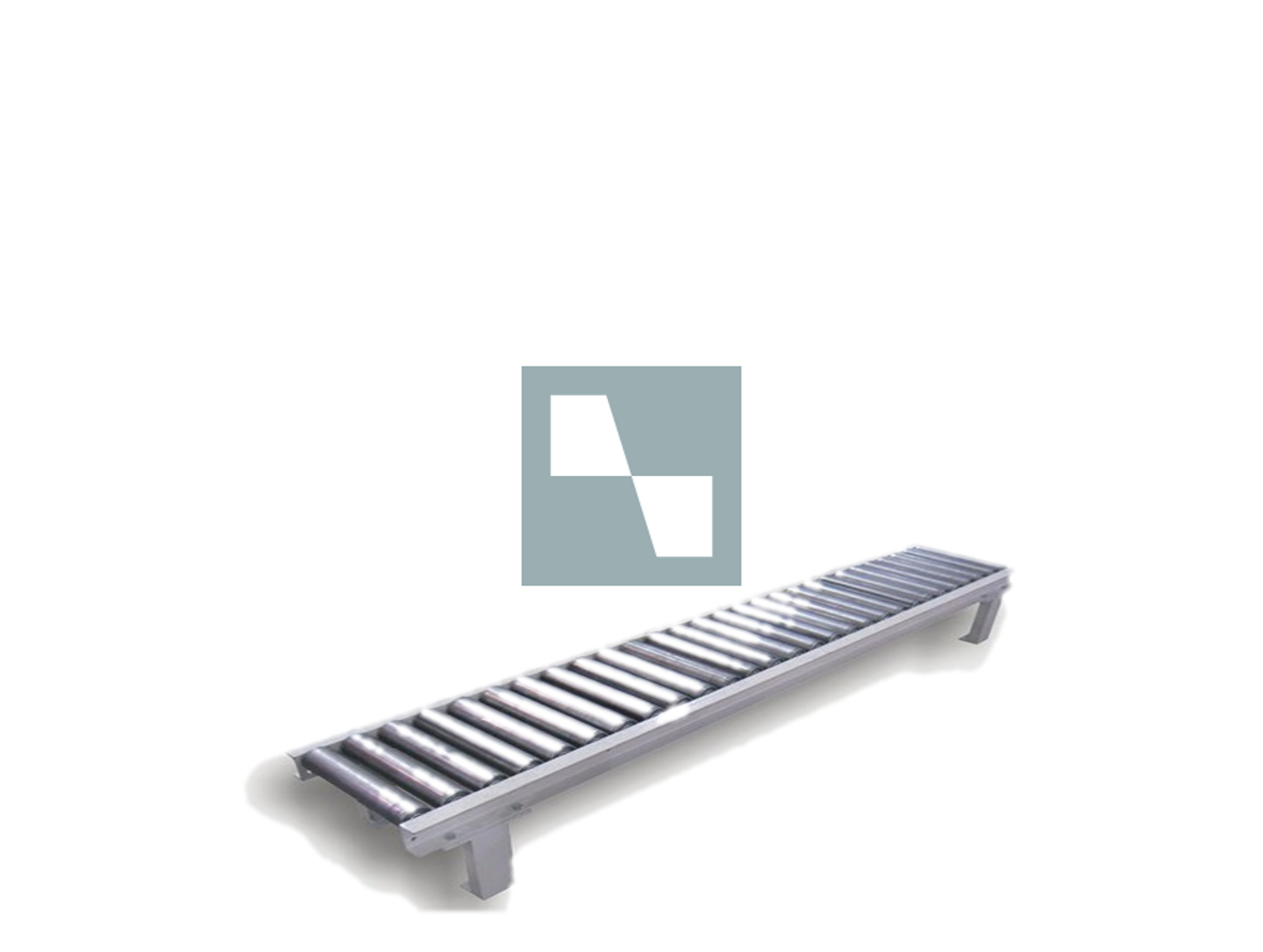
Gravity Roller Conveyor
Systec Conveyor’s Gravity Roller Conveyor (GRC) is the best built conveyor available. The features of Systec's GRC is the all-welded steel frame construction. Each piece is jig set and welded for exact position and tolerance. The heavy duty, structural steel side frame and tie-brace construction, is engineered for years of reliable service and will hold up under the most abusive environments. The GRC legs are also welded structural steel with laser cut top and bottom plates for precise fit.
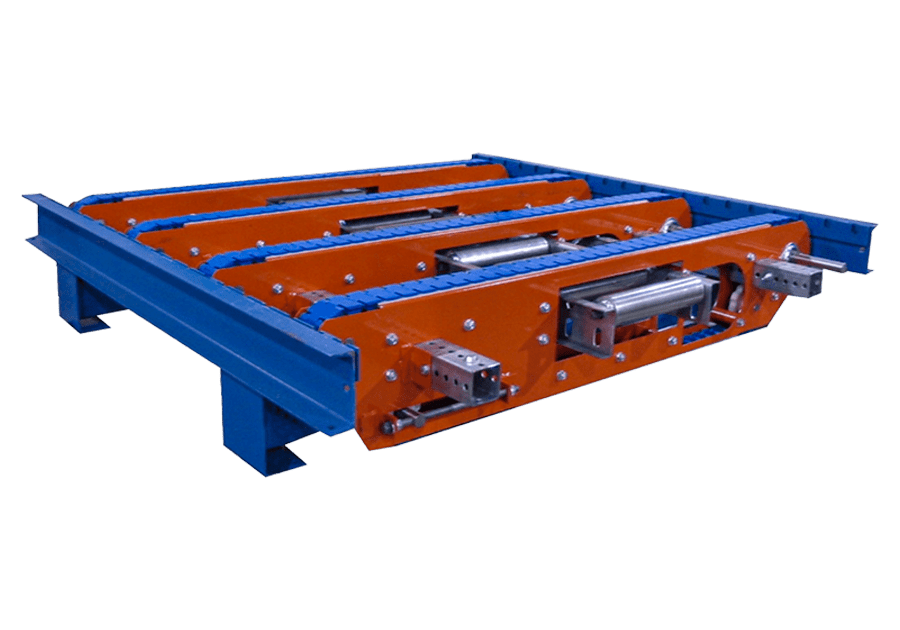
Belt Transfer Device
Systec’s Belt Transfer Device (BTD) is a safe and efficient method of moving loads onto and/or off of a conveyor line utilizing low-mark belts over chains. The features of Systec’s CTD allow it to sit within the conveyor line at various locations. It can be moved to nearly any location within the length of the conveyor line. It is totally independent of the conveyor in which it rests, and can be added to most other conveyor equipment manufacturers’ lines.
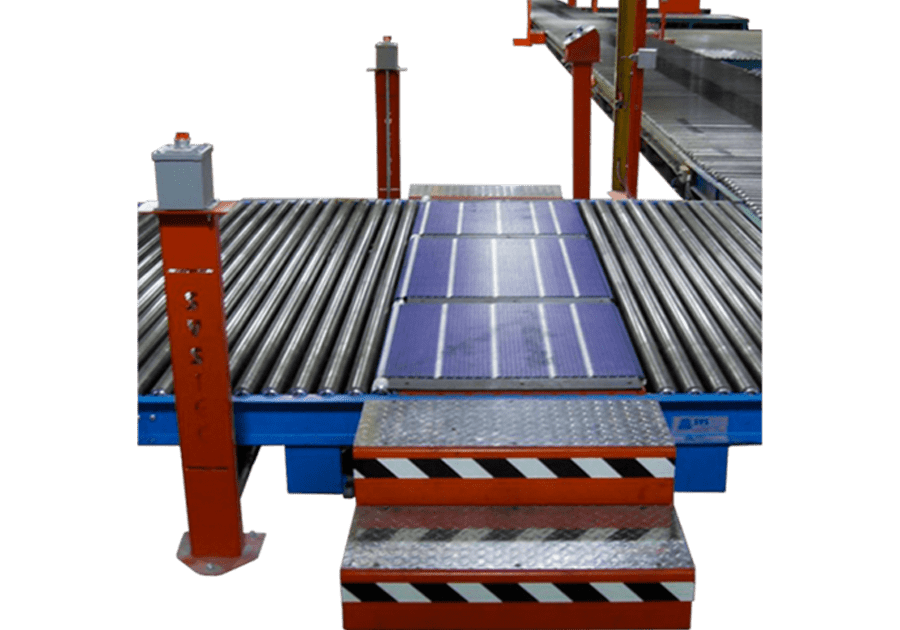
Conveyor Safe Walk (Safety)
Systec’s Conveyor Safe Walk (CSW) is a safe and efficient method of creating safe passage across any conveyor mainline. Based on the needs of the plant, the CSW can be incorporated into many different systems. Controls can be added to keep the CSW lane clear at all times, or it can be run with the push of a button. The CSW can sit within the new or existing conveyor line at various locations, and can be moved to nearly any location within the length of the conveyor line. The CSW is totally independent of the conveyor in which it rests, and can be added to all other conveyor equipment manufacturers’ lines as a stand-alone device.
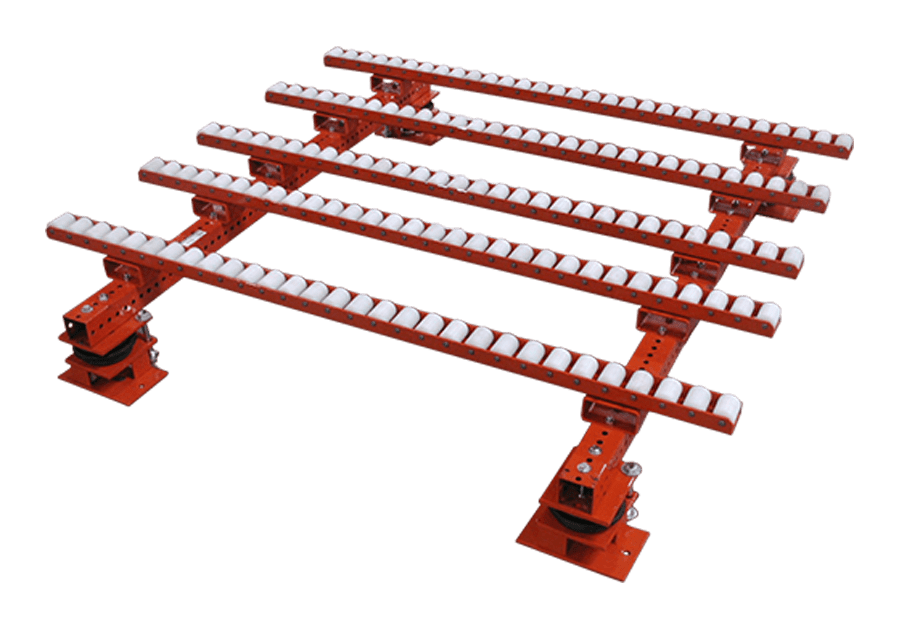
Roller Transfer Device
Systec’s Roller Transfer Device (RTD) is a very effective method of manual load movement on and/or off a conveyor line. Systec’s RTD design allows it to sit within the conveyor line at virtually any location. It can be moved, if need be, with very little effort. It is totally independent of the conveyor in which it rests, and can be added to most other conveyor equipment manufacturers’ lines. The RTD is capable of being added to a Powered Accumulating Roller conveyor (PAR), Powered Roller Only conveyor (PRO), or Gravity Roller Conveyor (GRC). Additionally, the RTD’s roller racks are fully adjustable on a 3" increment to meet any changes in load sizes or production requirements.
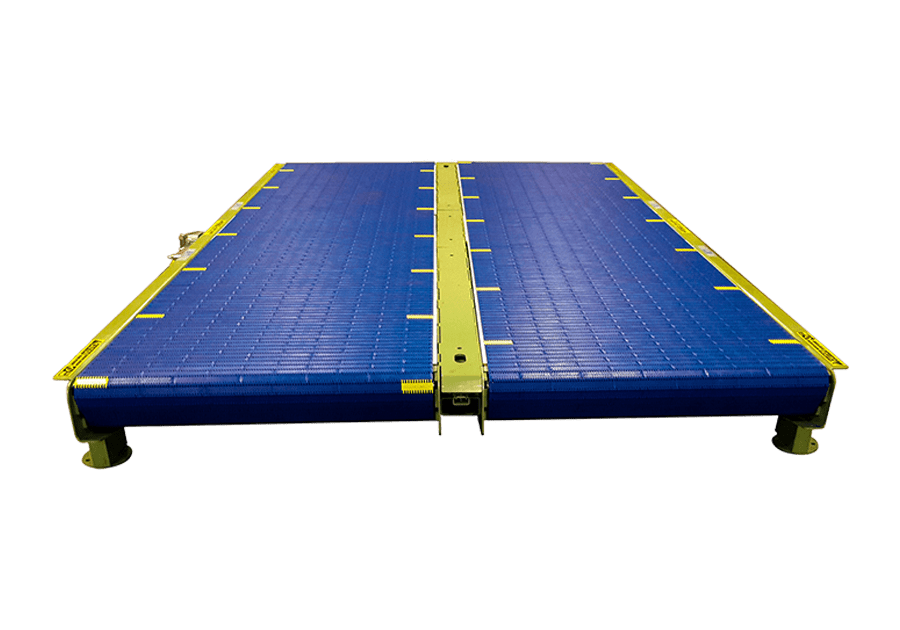
Stable Stack Conveyor
Systec’s StableStak Conveyor (SSC) is an independent conveyor line. SSC has several applications within a box plant. SSC is ideal for conveyance of loads at the corrugator discharge, where small blank handling is required. Additionally, SSC is a very suitable conveyor at a die-cut stacker for indexing loads discharged, or prior to the strapping or banding operation. At these locations, operators can walk on the conveyor’s smooth, solid surface.
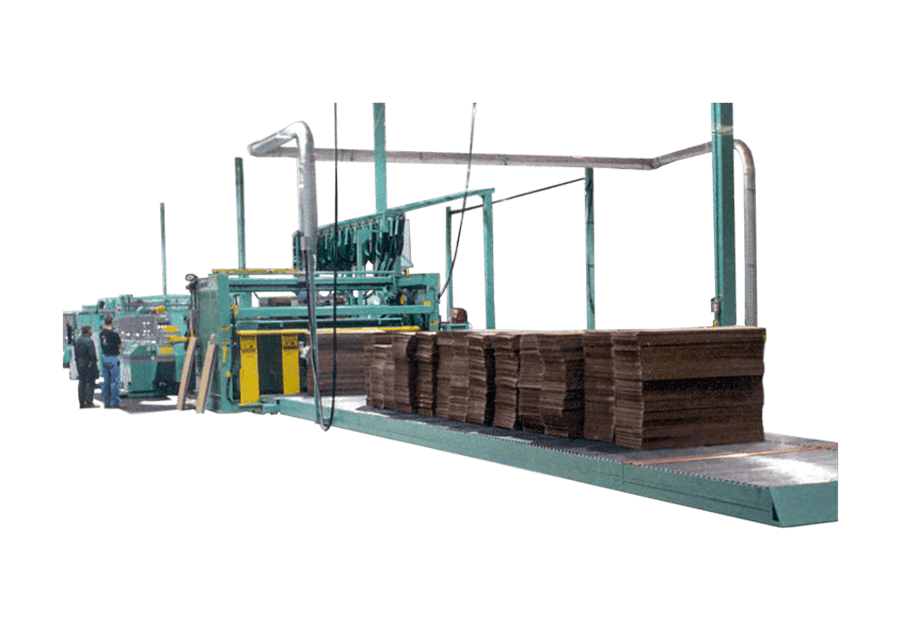
Mobile Infeed Conveyor
Our Mobil Infeed Conveyor (MIC) is designed for converting machine infeed and can move with the “roll-out” for maintenance and change-out. Its all-welded, steel frame construction, uses precision laser cut parts for exact fit and function. This is a very low maintenance device that applies the most advanced safety designs and features.

AutoFeed Robotic Feeding Solution
The AutoFeed Robotic Feeding Solution is responsible for transferring the corrugate material from the inbound conveyor system to the board feeder utilizing the end-of-arm tooling. Automatan AutoFeed systems have capability for 360kg and 750kg loads, and are designed for application on most commercially available FFG systems. The device consists of the robot, end-of-arm tool, backstop, and all associated controls to fully automate the loading process. The end-of-arm tool is responsible for segregating and securing a predetermined stack of corrugate material up to 14" in height during the transfer from the inbound conveyor system to the board feeder. Benefits include reduced manual labor, increased uptime and efficiency, a small footprint (it can save over 50% floor space from conventional pre-feeders), versatility (the ability to feed multiple machines), and six axes of motion to enable board flipping as well as nearly any layout configuration.
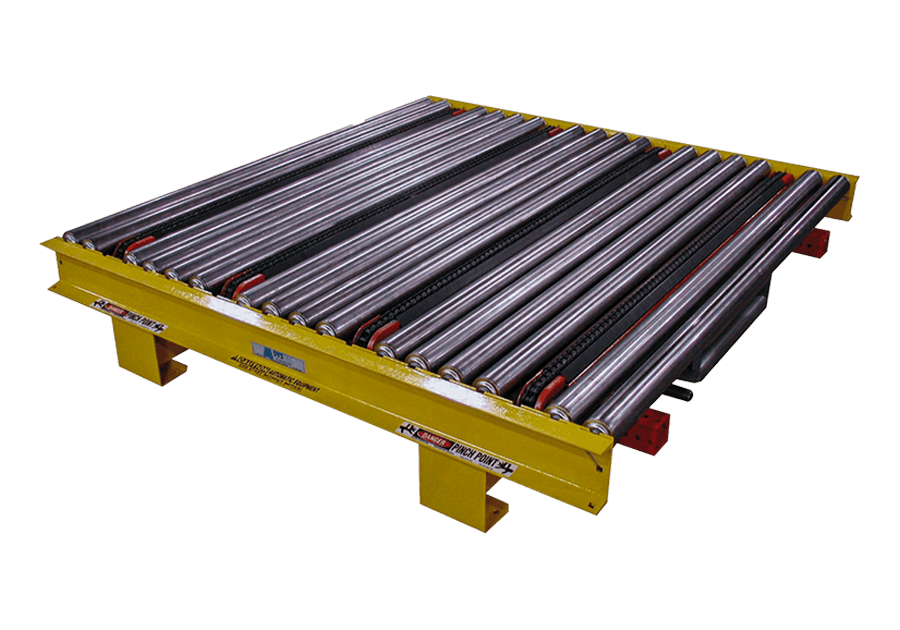
Chain Transfer Device
Systec’s Chain Transfer Device (CTD) is a safe and efficient method of moving loads onto and/or off of a conveyor line. The features of Systec’s CTD allow it to sit within the conveyor line at various locations. It can be moved to nearly any location within the length of the conveyor line. It is totally independent of the conveyor in which it rests, and can be added to most other conveyor equipment manufacturers’ lines. The CTD is capable of being added to either a Powered Accumulating Roller conveyor (PAR), Powered Roller Only conveyor (PRO), or Gravity Roller Conveyor (GRC). The device can act as a one-, two-, three-, or four-way intersection.
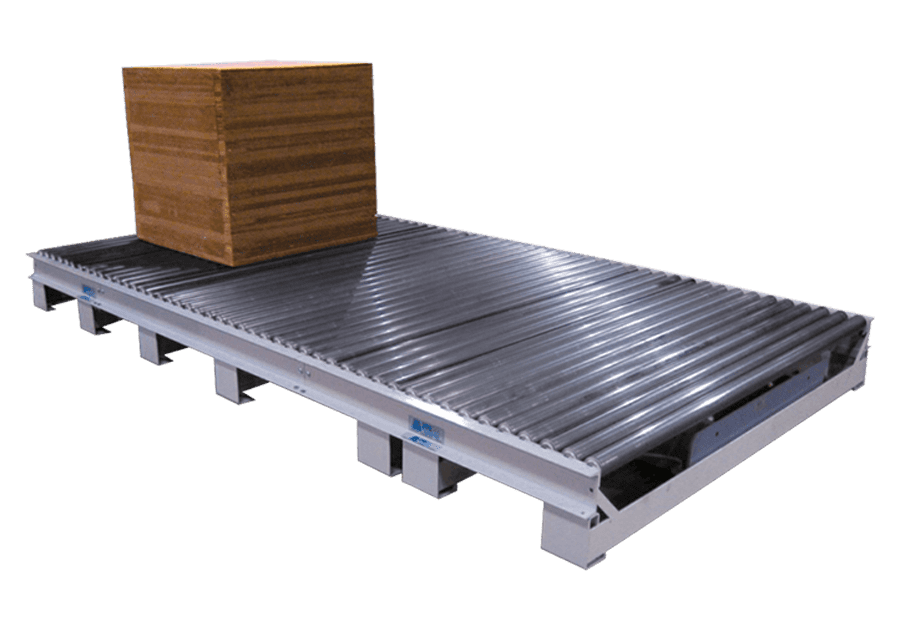
Powered Roller Conveyor
Systec’s Powered Roller Conveyor is provided as a powered accumulating roller (PAR) or a powered roller only (PRO) conveyor. The features of the PAR conveyor are the fully accumulating drive, take-up, and intermediate sections, or midsections. PAR conveyor allows loads to be added to a conveyor line without disruption or movement of loads already present on the line. With optional control features, loads can be added to the conveyor line until it is full, maximizing utilization of the entire conveyor line. Another control option would be multiple areas of accumulation, or zones, for loads to move independently and stage down the conveyor line. The accumulation features of PAR conveyor allow a single, one-horsepower drive to run up to 70' of conveyor. Systec’s PRO conveyor features a positive drive on the entire conveyor line and allows loads to be “indexed” as each load is added to the conveyor line.
Litho Labeling
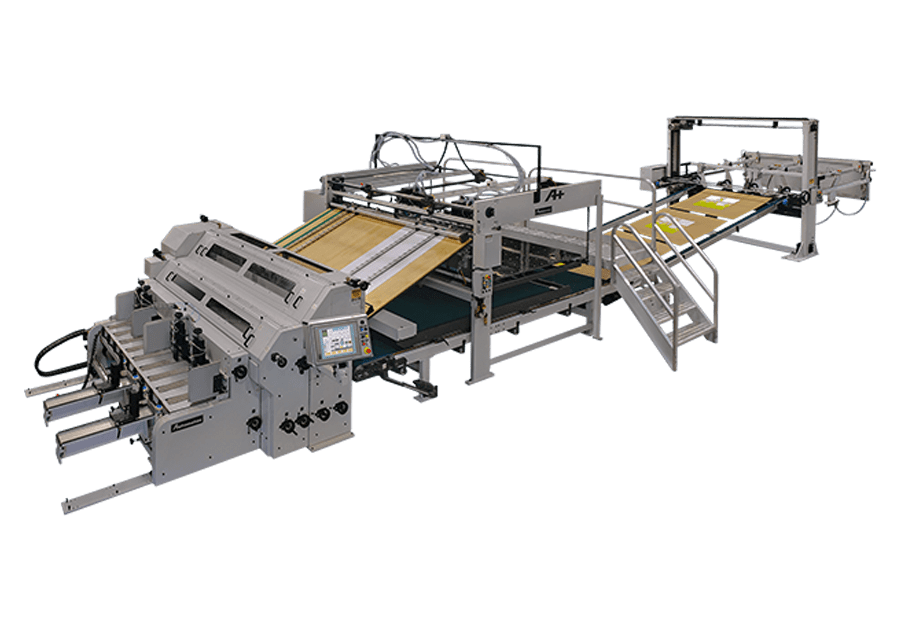
Model A+ Litho-Label Laminator
The Model A+ Lith0-Label Laminator is the newest member of the labeler family. The A+ offers the record-breaking ability to adhere an 81" (2055 mm) litho-label at speeds up to 6,000 sheets per hour utilizing its patented electrostatic application method. The A+ is versatile and dependable with single-face module, 6,000 sheets per hour, 81" x 65" litho label format, dual label/dual board, dynamic board registration, and standard water cleanup.
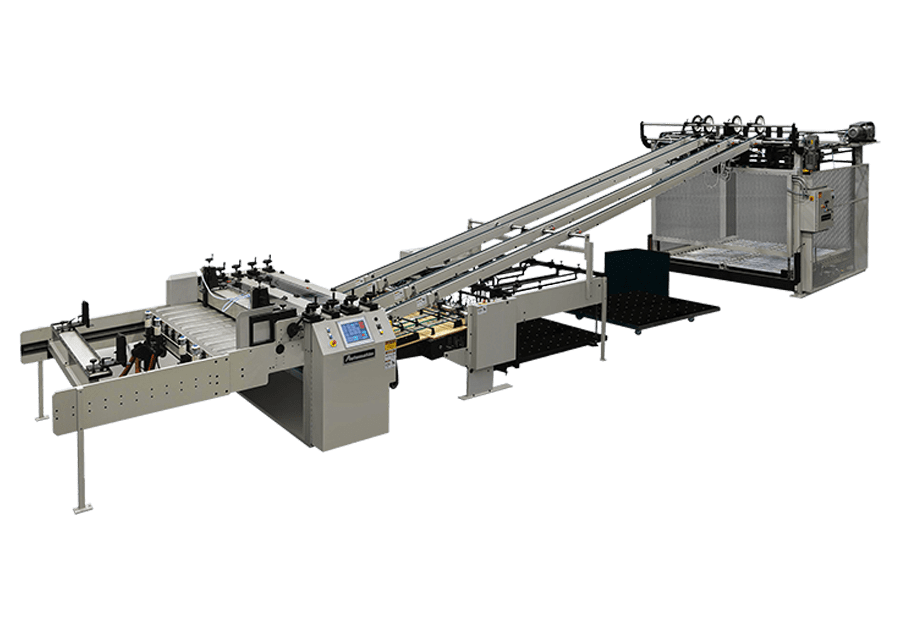
Model EM Litho-Label Laminator
The Automatan Model EM Litho-label Laminator applies Electrostatic Method technology in its adhesive application process. An economical labeler, the Model EM’s design offers the opportunity to employ the electrostatic method for fast, easy setups in labeling over a wide range of board and label sizes. The Automatan Model EM Litho-Label Laminator has been designed and configured as a versatile machine to be used in a variety of applications.
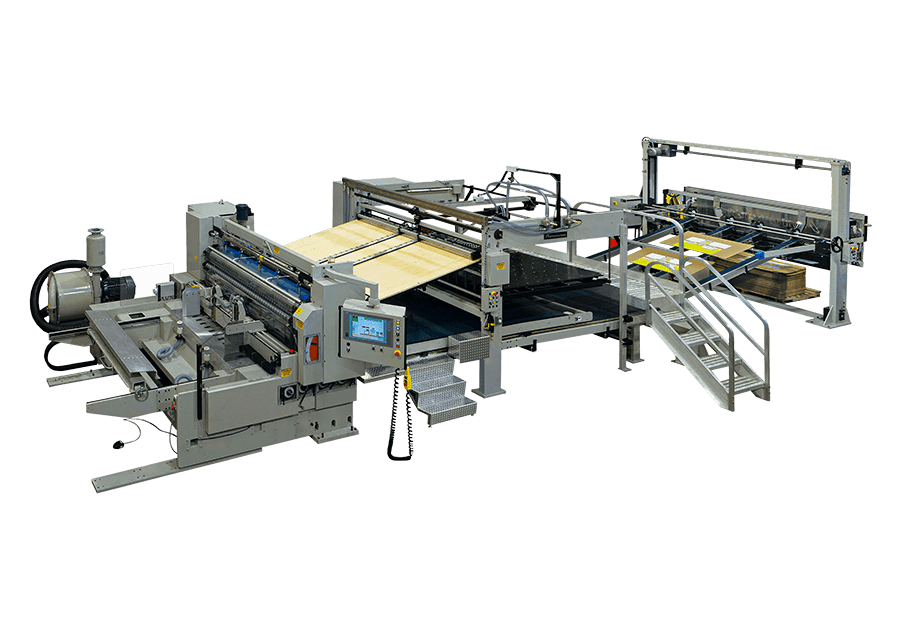
Model 8166 Litho-Label Laminator
The Automatan Model 8166 Litho-Label Laminator is shown with board feeder, laminating unit, label feeder and straight-through discharge to optional upstacker. This model full mounts or spot mounts litho-labels to double-face corrugated board. It delivers Large Format litho-labels (81" wide x 66" thru) with NO SKIP FEED operation required. A single-source drive controller simplifies the electrical system design and operating programs. A display panel provides the operator with easy-to-use menus and screens for fingertip control of the laminating process. The Model 8166 has stationary machine components with tilt-down transfer units to allow easy access for machine setup, equipment additions, cleanup and routine maintenance.
Take Off/Out Feed
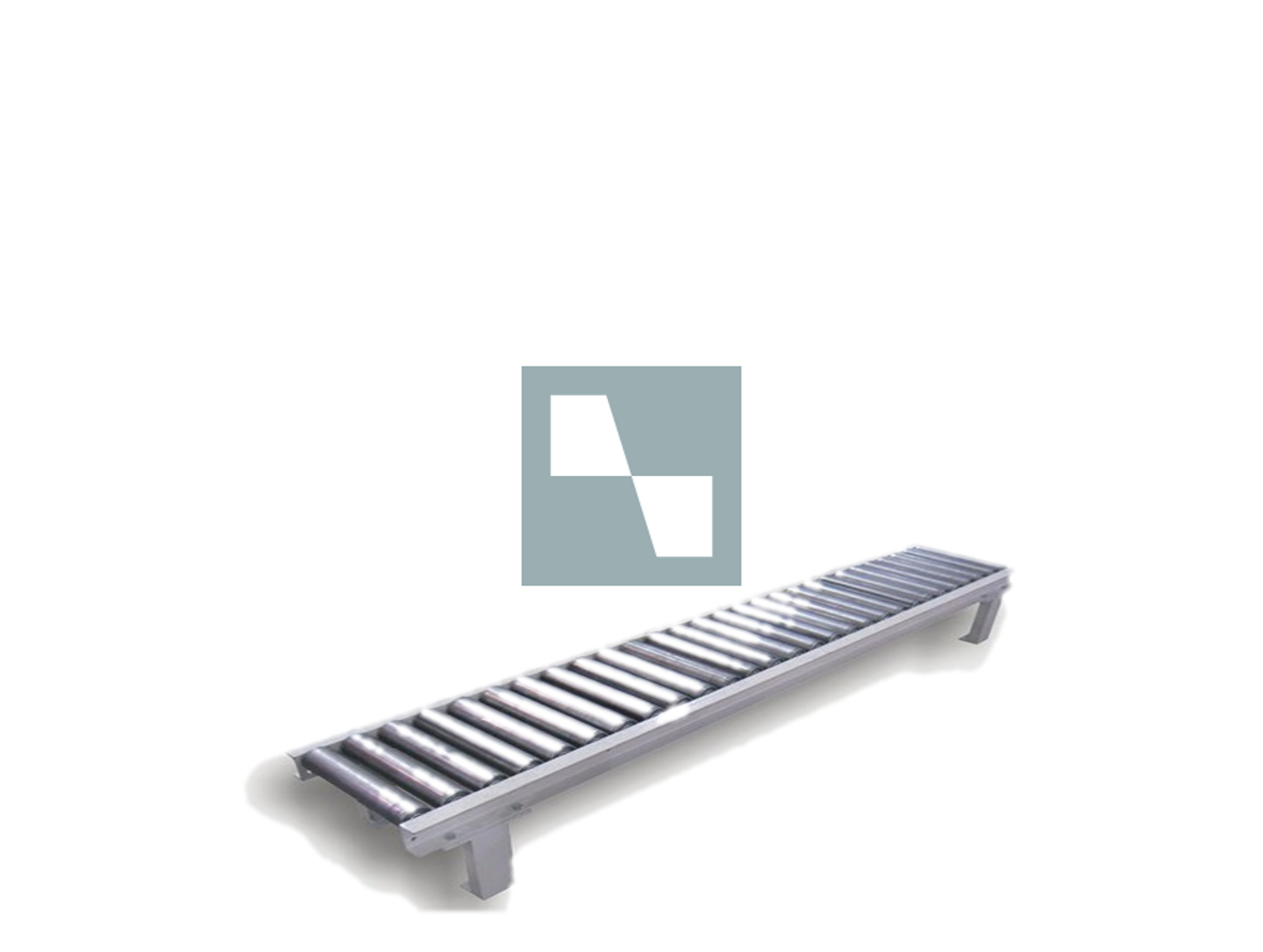
Gravity Roller Conveyor
Systec Conveyor’s Gravity Roller Conveyor (GRC) is the best built conveyor available. The features of Systec's GRC is the all-welded steel frame construction. Each piece is jig set and welded for exact position and tolerance. The heavy duty, structural steel side frame and tie-brace construction, is engineered for years of reliable service and will hold up under the most abusive environments. The GRC legs are also welded structural steel with laser cut top and bottom plates for precise fit.
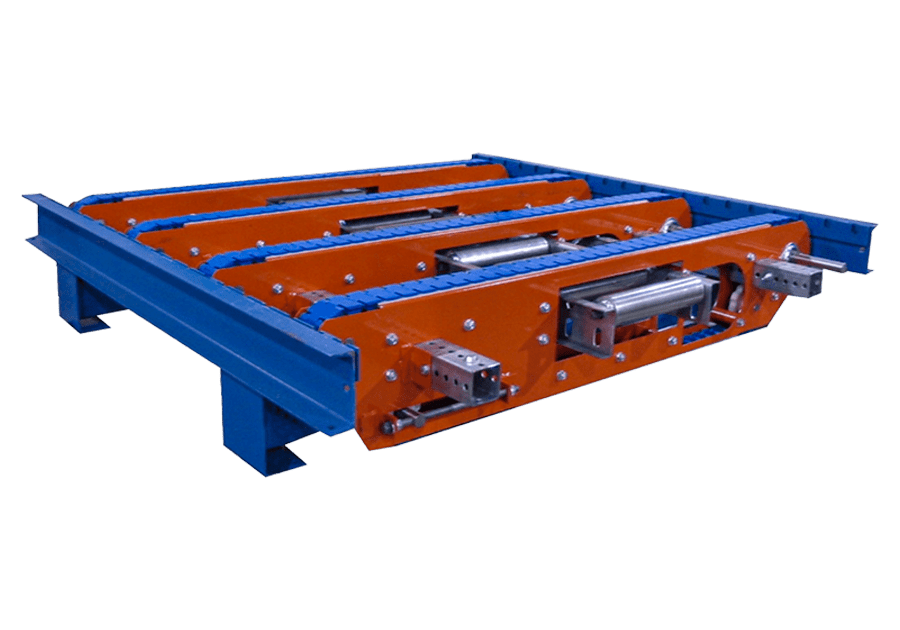
Belt Transfer Device
Systec’s Belt Transfer Device (BTD) is a safe and efficient method of moving loads onto and/or off of a conveyor line utilizing low-mark belts over chains. The features of Systec’s CTD allow it to sit within the conveyor line at various locations. It can be moved to nearly any location within the length of the conveyor line. It is totally independent of the conveyor in which it rests, and can be added to most other conveyor equipment manufacturers’ lines.
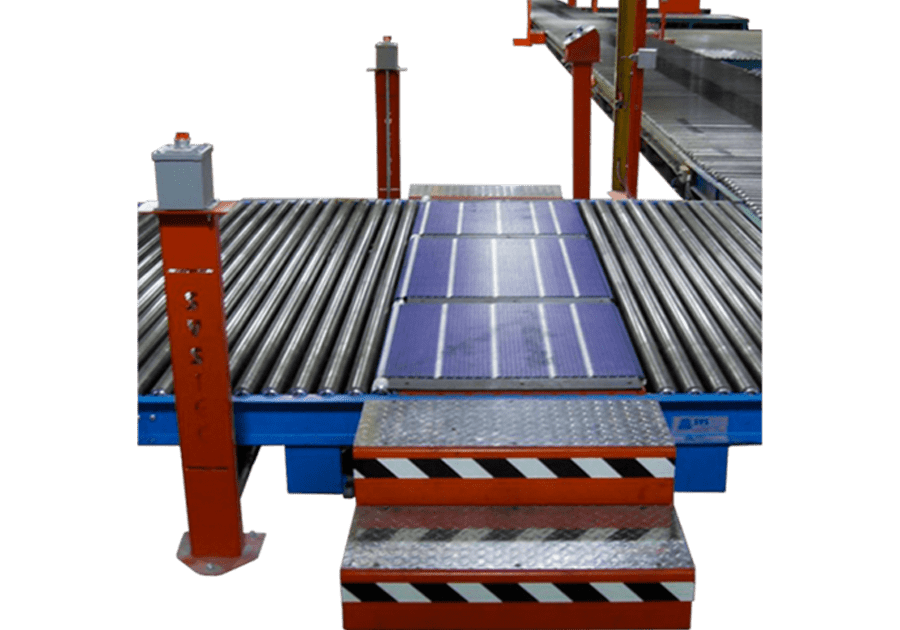
Conveyor Safe Walk (Safety)
Systec’s Conveyor Safe Walk (CSW) is a safe and efficient method of creating safe passage across any conveyor mainline. Based on the needs of the plant, the CSW can be incorporated into many different systems. Controls can be added to keep the CSW lane clear at all times, or it can be run with the push of a button. The CSW can sit within the new or existing conveyor line at various locations, and can be moved to nearly any location within the length of the conveyor line. The CSW is totally independent of the conveyor in which it rests, and can be added to all other conveyor equipment manufacturers’ lines as a stand-alone device.
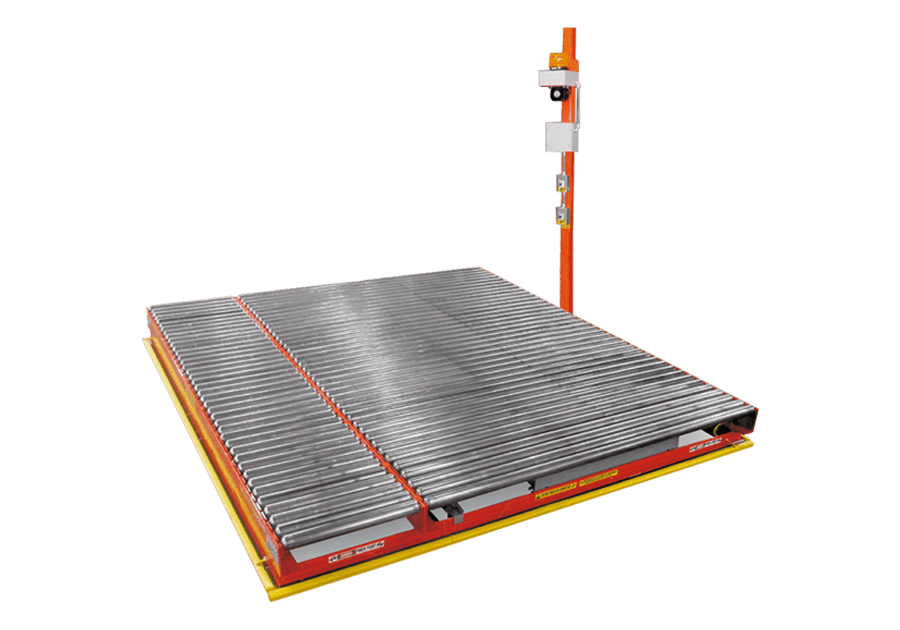
Side Pivot Conveyor
Systec’s Side Pivot Conveyor (SPC) can be used at various points within the overall conveyor system. The SPC is primarily used where change in load direction is required, yet the load orientation must remain the same. This is particularly applicable where pallets may be used within the system. This is due to the fact that the pallet’s runners, or bottom boards, must remain perpendicular to the load-carrying rollers to smoothly convey the load. The SPC is applicable at points within a conveyor line where pivoting around an obstacle, such as a building column, is required. It can also be used at a location where a break in the line may be required for equipment, such as a forklift, to gain access to an area inside the conveyor system. Each SPC is provided with a floor-mounted mast assembly with power disconnect switches and an audible and strobe-light warning system for impending conveyor movement. It also provides the necessary power for the conveyor and pivoting movement.
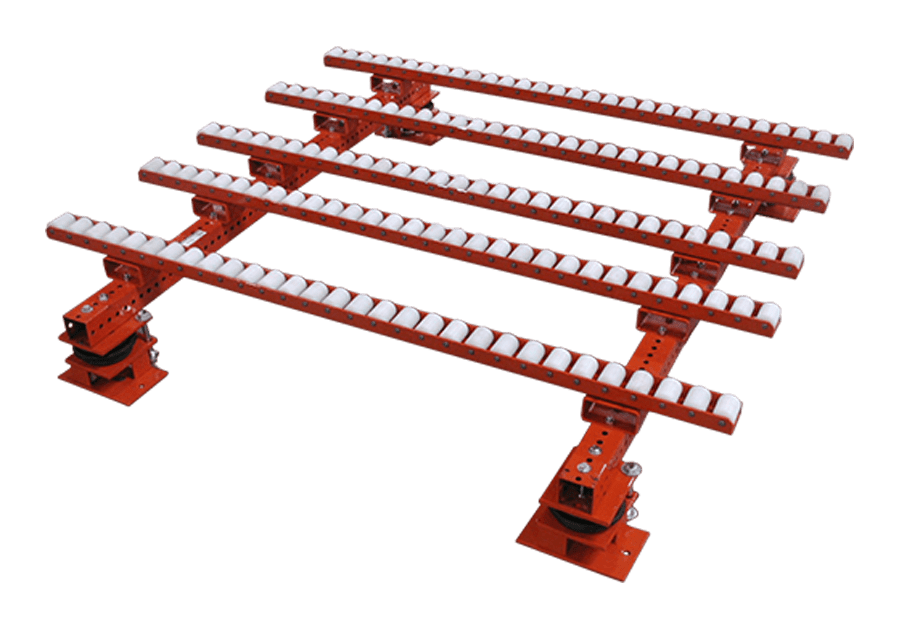
Roller Transfer Device
Systec’s Roller Transfer Device (RTD) is a very effective method of manual load movement on and/or off a conveyor line. Systec’s RTD design allows it to sit within the conveyor line at virtually any location. It can be moved, if need be, with very little effort. It is totally independent of the conveyor in which it rests, and can be added to most other conveyor equipment manufacturers’ lines. The RTD is capable of being added to a Powered Accumulating Roller conveyor (PAR), Powered Roller Only conveyor (PRO), or Gravity Roller Conveyor (GRC). Additionally, the RTD’s roller racks are fully adjustable on a 3" increment to meet any changes in load sizes or production requirements.
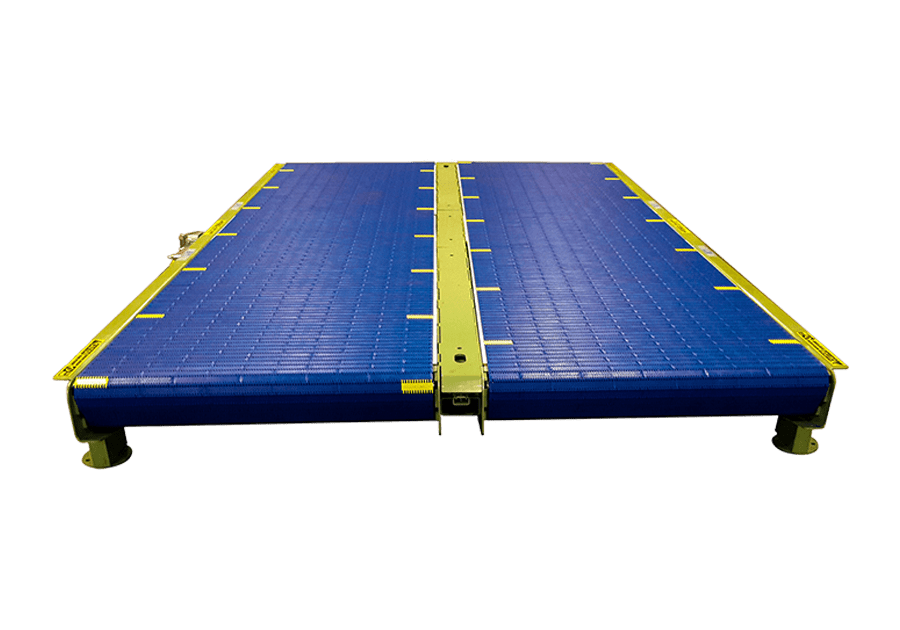
Stable Stack Conveyor
Systec’s StableStak Conveyor (SSC) is an independent conveyor line. SSC has several applications within a box plant. SSC is ideal for conveyance of loads at the corrugator discharge, where small blank handling is required. Additionally, SSC is a very suitable conveyor at a die-cut stacker for indexing loads discharged, or prior to the strapping or banding operation. At these locations, operators can walk on the conveyor’s smooth, solid surface.
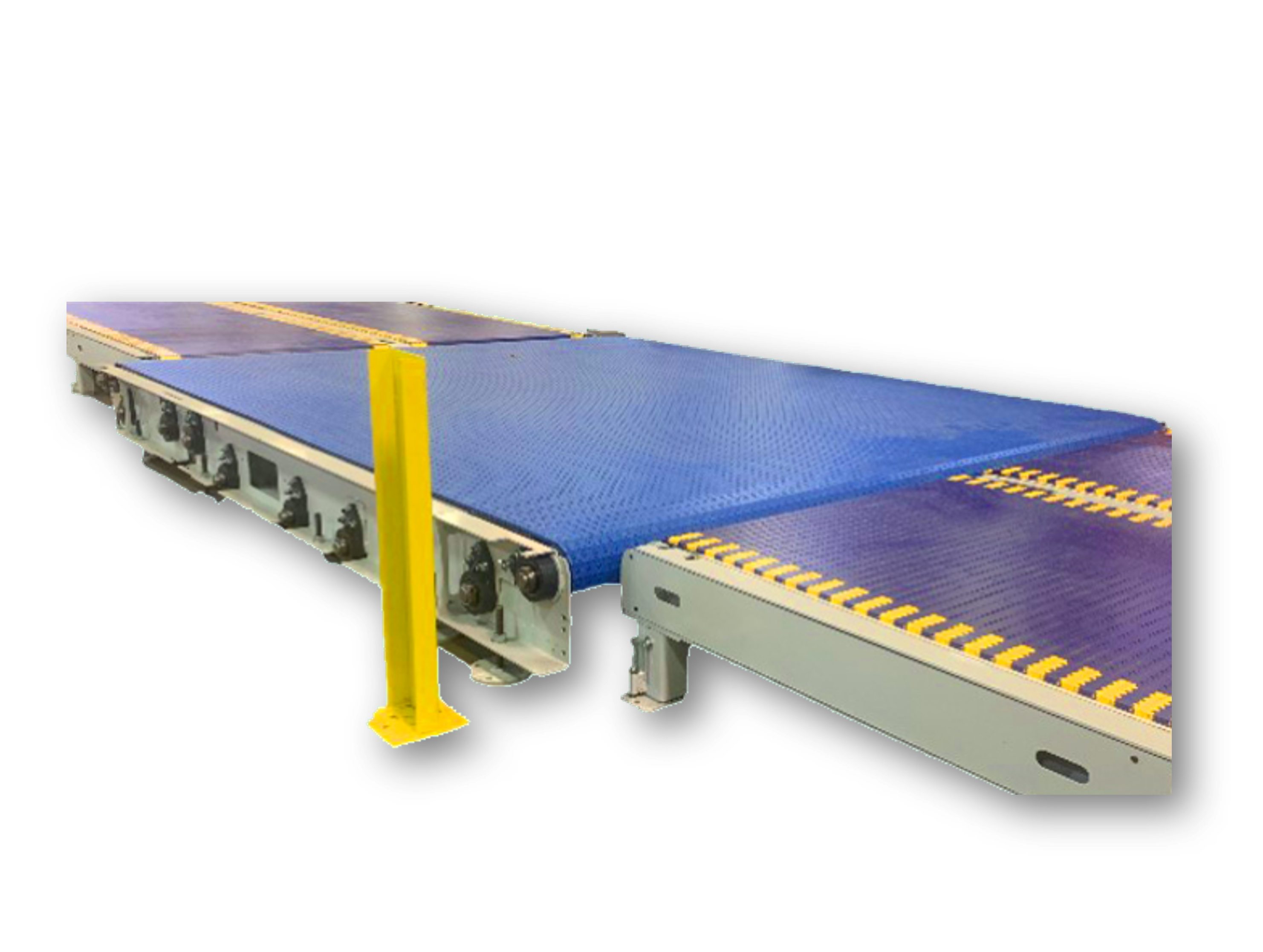
Acitve Ball Belt Rotation Device
Systec’s Active Ball Rotation Device (ABRD) utilizes the latest technology of Active Ball belt to provide a very effective method of rapid and precise load rotation. While similar in function to the Load-Rotation Device (LRD), the ABRD can rotate loads more quickly and effectively since independent devices to lift and rotate the loads are not present. The rotation feature has been maximized for efficiency and accuracy.
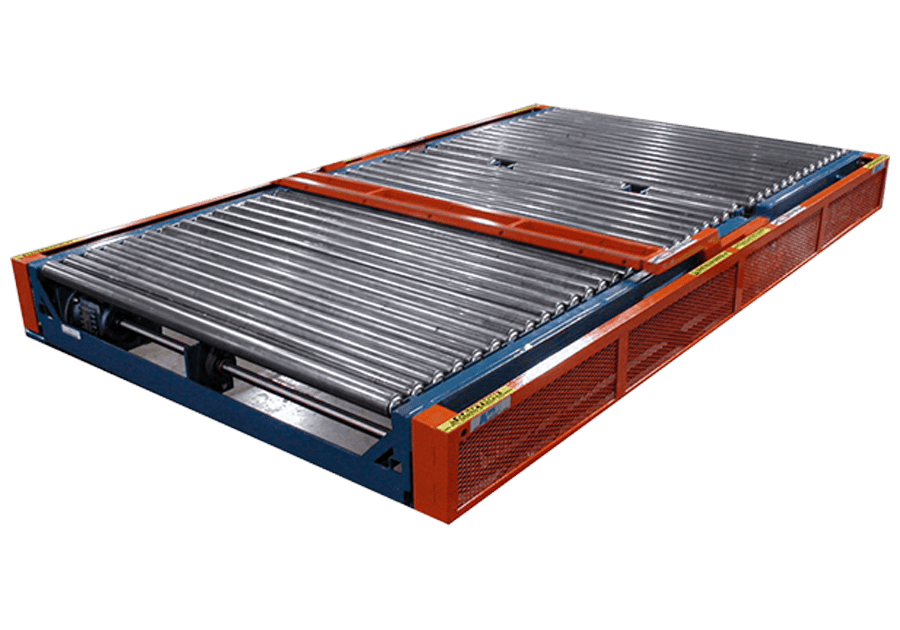
Pop-Up Infeed
Systec’s Pop-Up Infeed Device (PID) is an integral part of the conveyor line. Typically, it is used at the end of a conveyor line for transfer of a load off the line, onto a perpendicular conveyor line, or simply off the line onto a pallet, cart, or some other transport method. Systec’s Sheet Gripping Device (SGD) can be used at the end of the PID for transferring loads onto deck, or bottom dunnage sheets. The over-stroke capabilities of this device ensure the load will not only be transferred fully off the conveyor line but a full 9" beyond the end of the line. The PID can be used in Powered Accumulating Roller conveyor (PAR), Powered Roller Only conveyor (PRO), or Gravity Roller Conveyor (GRC) applications.
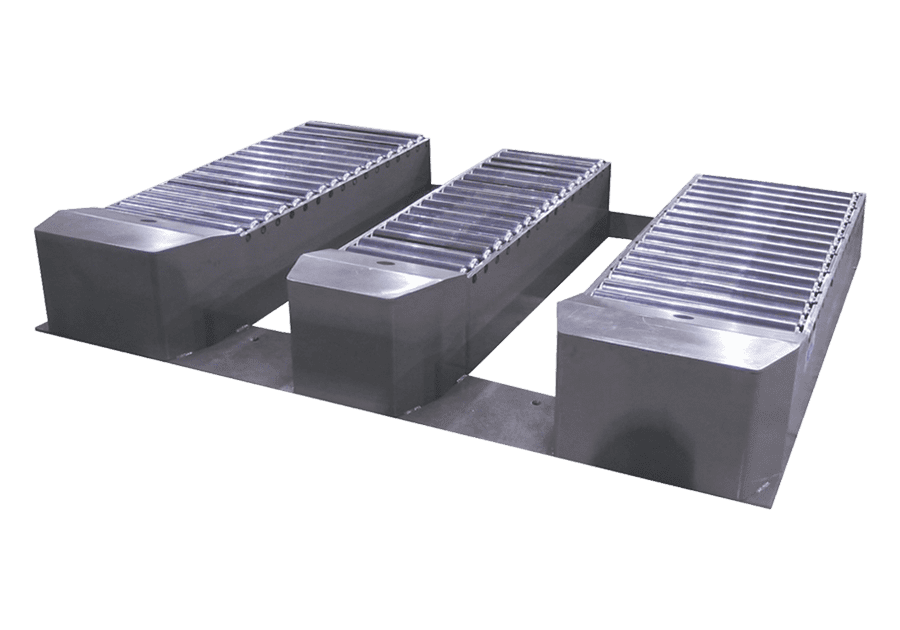
Fork Truck Interface
The Fork Truck Interface provides a set location for fork trucks to interface with conveyor equipment. The Interface consists of three independent units that can be combined to address any fork truck interface need. Systec’s Fork Truck Station provides extra stability to equipment by being mounted into concrete floor. There are several options for Fork Truck Stations, including gravity rollers, powered roller, powered StableStak plastic mesh top, side entry and individual fingers. Systec’s Fork Truck Ramp provides a smooth surface for the forks of a lift truck to easily slide under the load for retrieval.
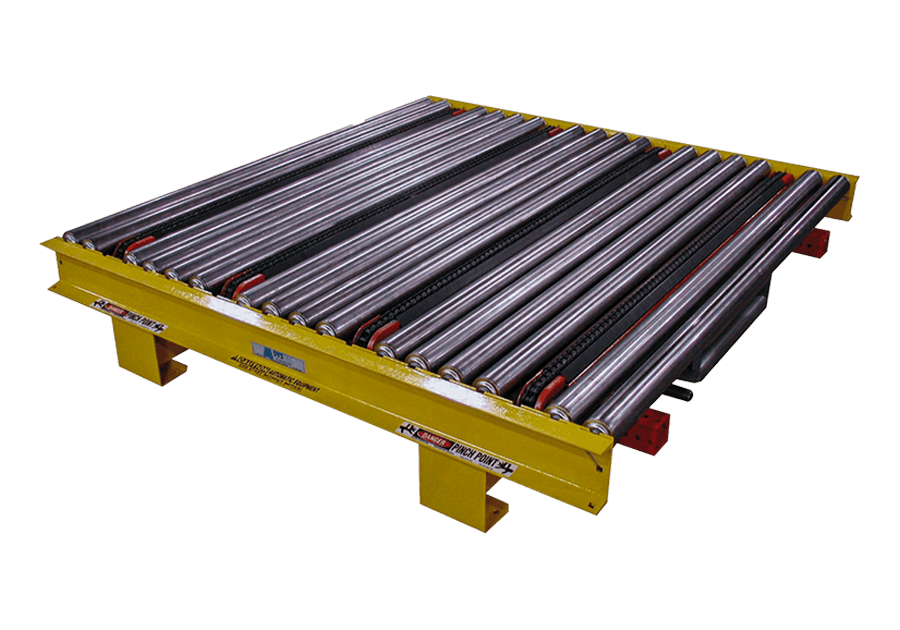
Chain Transfer Device
Systec’s Chain Transfer Device (CTD) is a safe and efficient method of moving loads onto and/or off of a conveyor line. The features of Systec’s CTD allow it to sit within the conveyor line at various locations. It can be moved to nearly any location within the length of the conveyor line. It is totally independent of the conveyor in which it rests, and can be added to most other conveyor equipment manufacturers’ lines. The CTD is capable of being added to either a Powered Accumulating Roller conveyor (PAR), Powered Roller Only conveyor (PRO), or Gravity Roller Conveyor (GRC). The device can act as a one-, two-, three-, or four-way intersection.
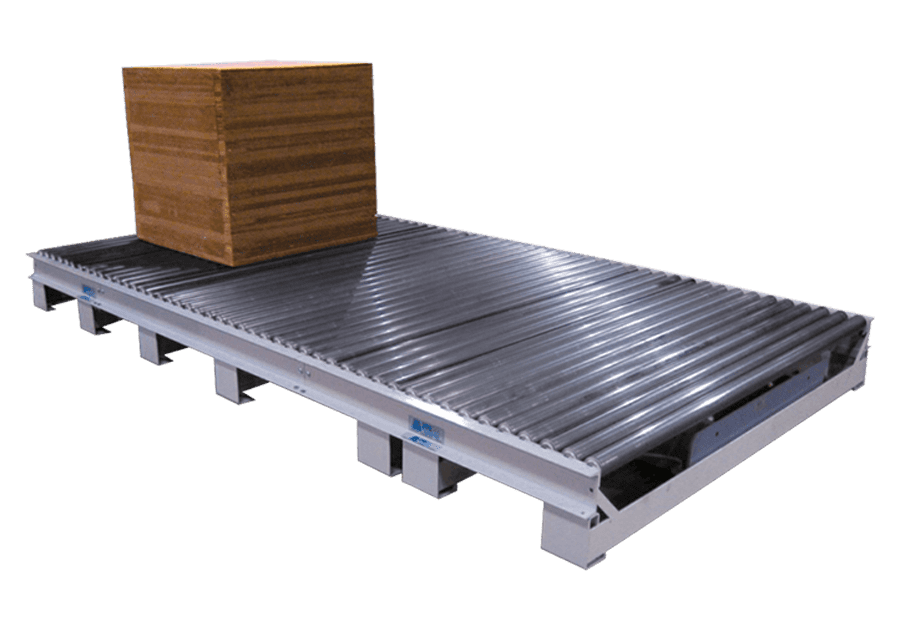
Powered Roller Conveyor
Systec’s Powered Roller Conveyor is provided as a powered accumulating roller (PAR) or a powered roller only (PRO) conveyor. The features of the PAR conveyor are the fully accumulating drive, take-up, and intermediate sections, or midsections. PAR conveyor allows loads to be added to a conveyor line without disruption or movement of loads already present on the line. With optional control features, loads can be added to the conveyor line until it is full, maximizing utilization of the entire conveyor line. Another control option would be multiple areas of accumulation, or zones, for loads to move independently and stage down the conveyor line. The accumulation features of PAR conveyor allow a single, one-horsepower drive to run up to 70' of conveyor. Systec’s PRO conveyor features a positive drive on the entire conveyor line and allows loads to be “indexed” as each load is added to the conveyor line.
Palletizing

Pallet Sweep Device
Systec’s Pallet Sweep Device (PSD) is an efficient way to remove corrugated loads from pallets to infeed a machine. After the palleted load enters a zone, the pusher head is engaged and pushes the load off the pallet and onto the corresponding conveyor line. The load is then sent on for additional processing. After the head returns to the home position, the empty pallet is moved up the initial conveyor line to be cleared. Each system is custom designed for directional layout, pallet retrieval methods, operational controls, cycle times, and multiple pallet sizes and types.
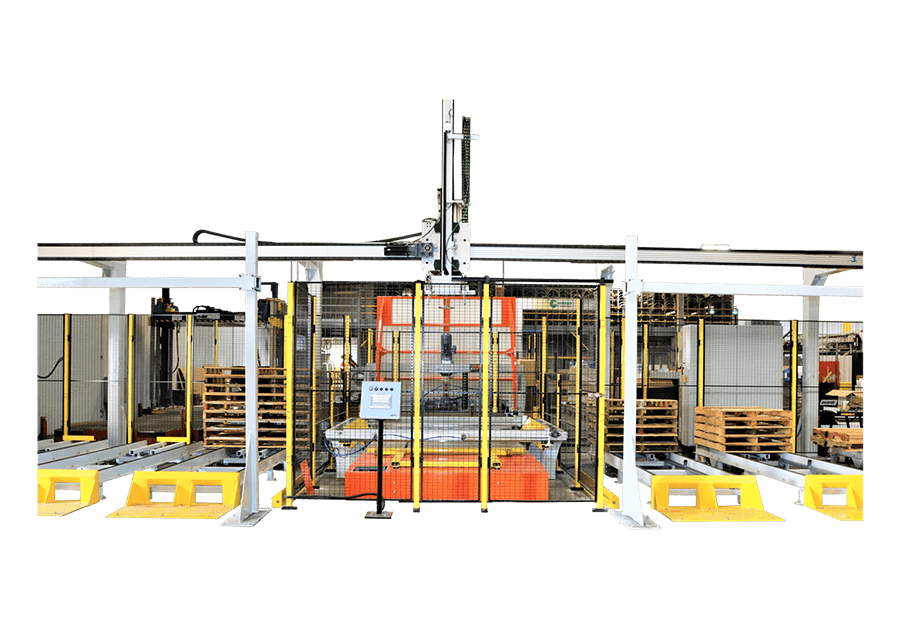
LPD Load Palletizing Device & Fast Pal (by Avanti)
The device is designed to square, center and lift finished loads for placement on pallets. Constructed from high-quality components and assemblies, the LPD is designed for precision transfer of complete loads to pallets utilizing the squaring heads. The LPD can be designed to accommodate from 78.74" to 141.73" in through length of the sides of the machine. When combined with the FastPal robotic pallet retrieval system, this automated warehousing solution is able to maintain a high palletizing volume.
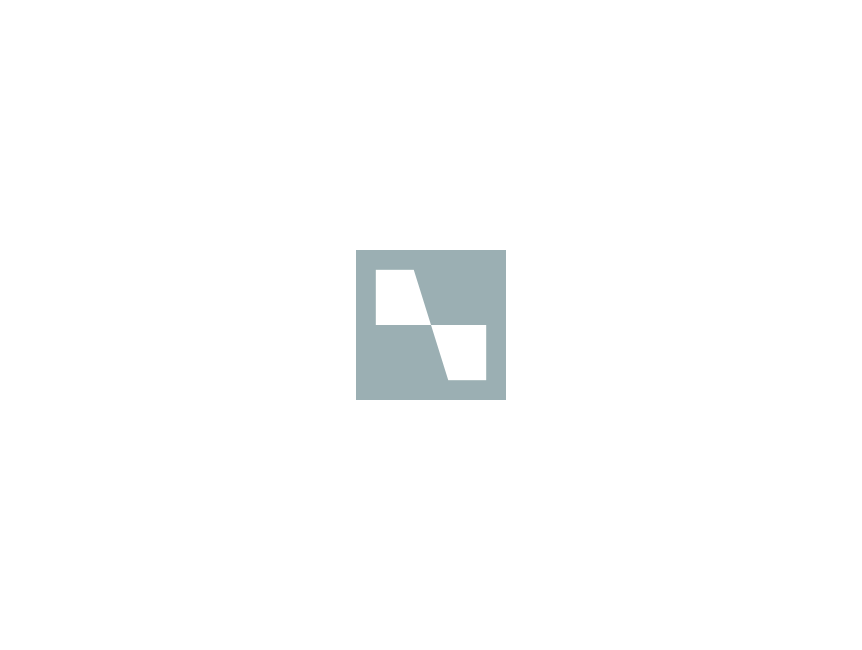
Base Pad Inserter
The Base Pad Inserter is used in corrugated or solid board factories where, for whatever reason, pads need to be introduced under a load to be automatically strapped with or without a pallet. These pads give protection to the load from the straps applied to the load to hold it secure, with or without a pallet. The unit can be used when the load is strapped before being placed on a pallet. The pads are scored to suit the customer and placed under the load in position along the length of the load and protruding by about 100mm (4''). This 100mm (4'') folds up in the palletizer on the score and acts as protection to the load edges where the straps are applied.

AutoStak Robotic Load Former
The AutoStak Robotic Load Former is responsible for transferring bundles of corrugated material from the inbound conveyor system to an Automatan or customer-supplied load former utilizing the End-of-Arm Tool (EOAT) and custom programming. The AutoStak Palletizing EOAT is responsible for transferring the corrugate bundles from the outbound conveyor system to the palletizing area utilizing paddles. The AutoStak conveyor section will justify the bundle to the proper position on the conveyors, move the bundle into the AutoStak robotic bundle feed section, and then assist the robot in transferring the bundle into the Automatan’s or the plant’s load former, in the proper position for each specific layer pattern.
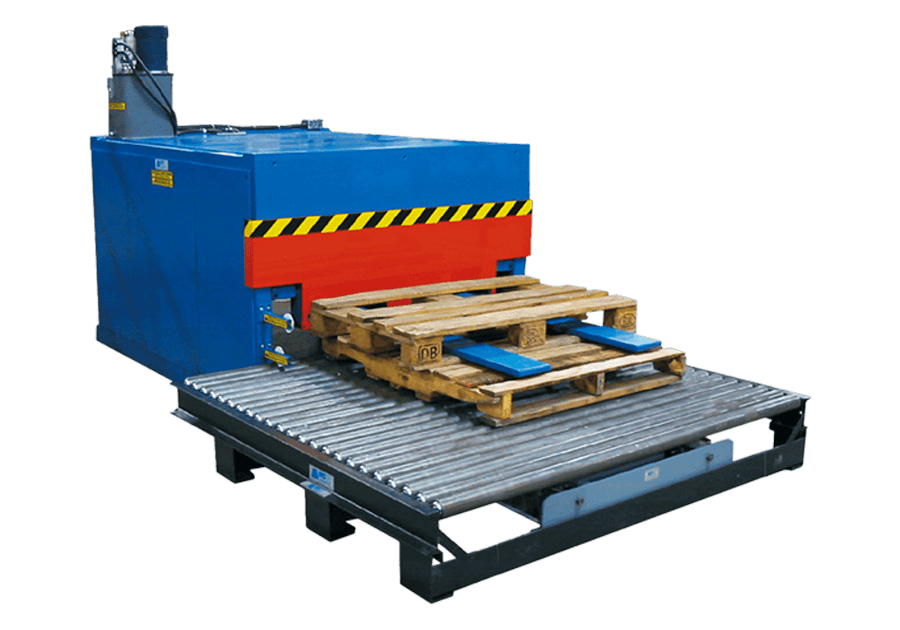
Pallet Handling
Systec has several devices designed to assist with pallet management and load position. These inlcude the Pallet Load Unit Stacker, Pallet Handling Device, Pallet Loading Device, and Pallet Sweep Device.
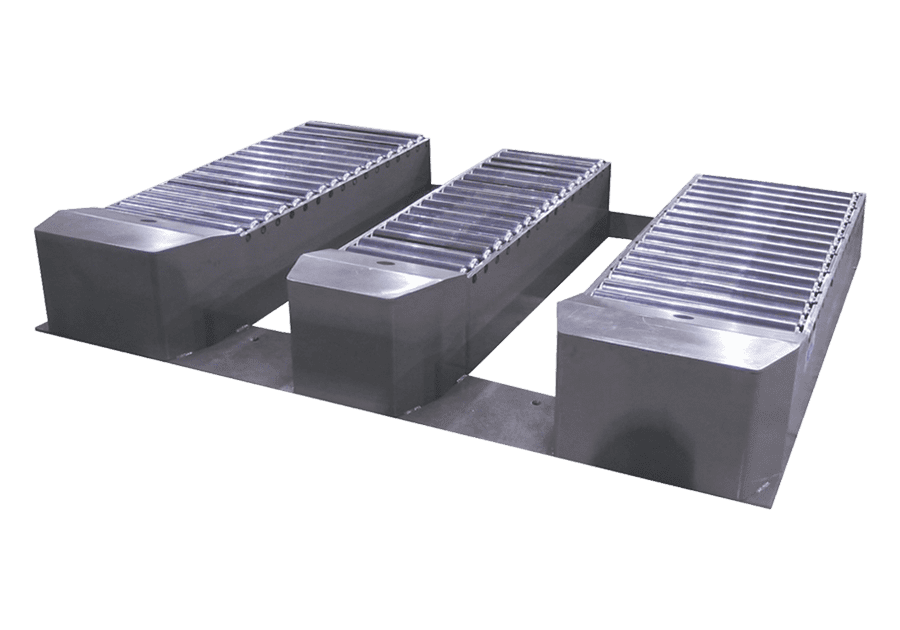
Fork Truck Interface
The Fork Truck Interface provides a set location for fork trucks to interface with conveyor equipment. The Interface consists of three independent units that can be combined to address any fork truck interface need. Systec’s Fork Truck Station provides extra stability to equipment by being mounted into concrete floor. There are several options for Fork Truck Stations, including gravity rollers, powered roller, powered StableStak plastic mesh top, side entry and individual fingers. Systec’s Fork Truck Ramp provides a smooth surface for the forks of a lift truck to easily slide under the load for retrieval.
Unitizer Controls
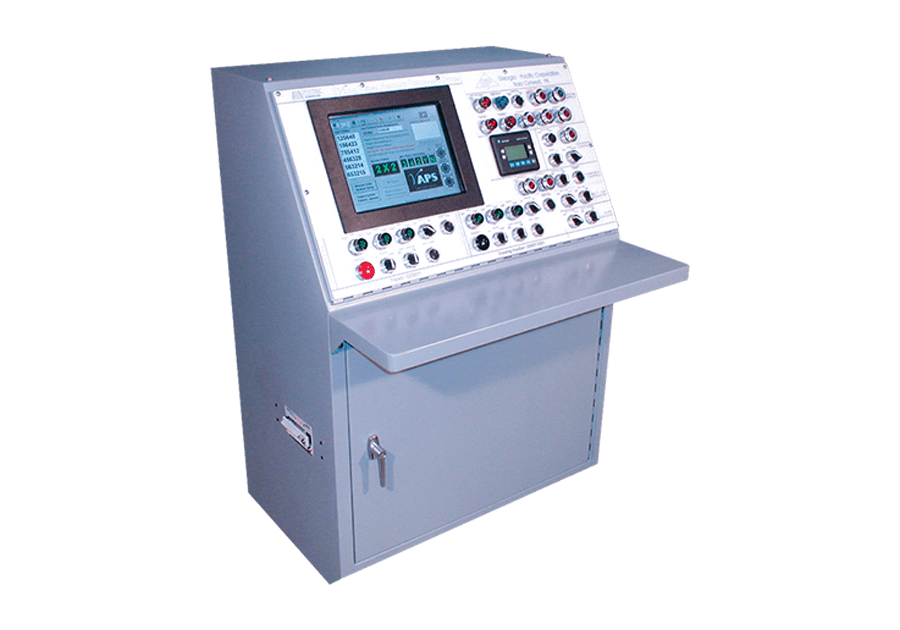
Visual Absolute Positioning System (VAPS)
Systec’s Visual Absolute Positioning System (VAPS) is custom engineered to enhance strapper or unitizer operation capabilities, simplify the operator’s interface, and increase production throughput. VAPS comes standard with either a telephone modem or internet-based interface, which allows off-site support. It utilizes a “teachable” control system that allows operators to input an unlimited number of custom strapping patterns based on a specific order requirement. The system is fully customizable for any strapping patterns, and can be set for up to 21 primary and 12 cross strap options.
Software
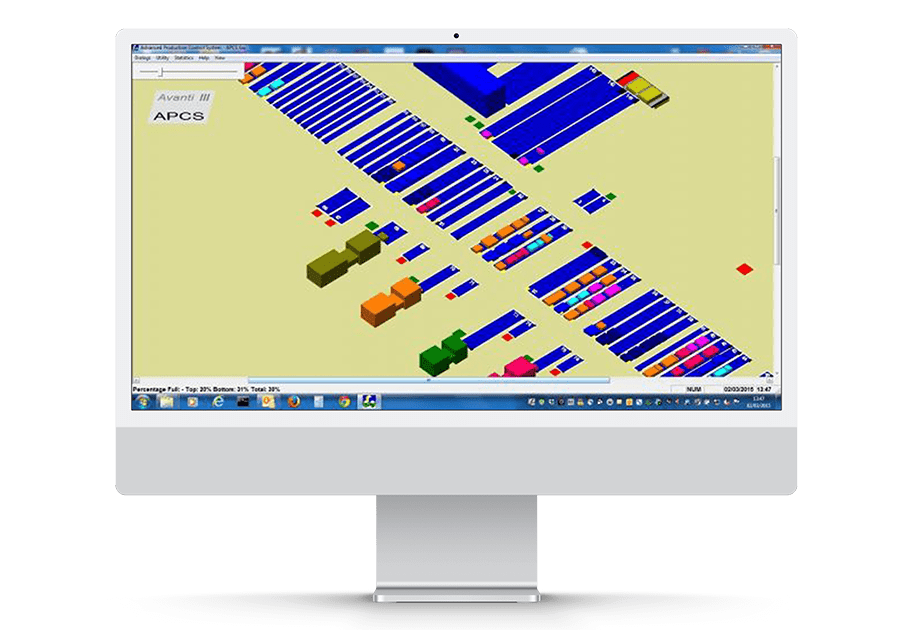
APICS (Automated Production Control System)
The Automated Production Control System (APICS) is a comprehensive WIP management system that integrates with the plant’s scheduling system. It simply requires a server to run the software and three work stations—one near the corrugator, one near the conversion machine, and the other with the planner. Each machine is color coded for easy tracking. The system tracks and monitors position and status for each load within the WIP system. Systec is the licensed provider and servicer for APICS in North America.
Work in Process
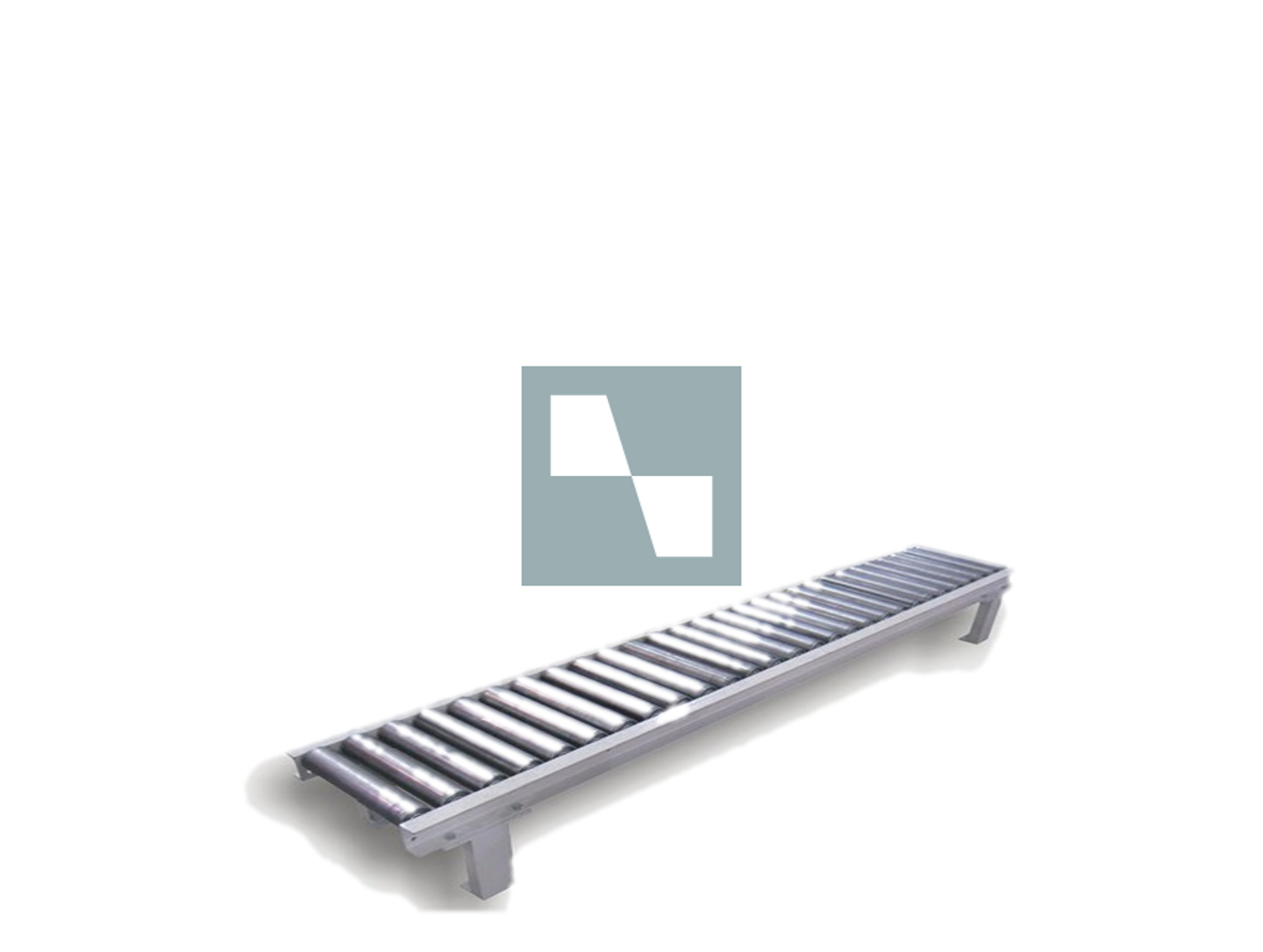
Gravity Roller Conveyor
Systec Conveyor’s Gravity Roller Conveyor (GRC) is the best built conveyor available. The features of Systec's GRC is the all-welded steel frame construction. Each piece is jig set and welded for exact position and tolerance. The heavy duty, structural steel side frame and tie-brace construction, is engineered for years of reliable service and will hold up under the most abusive environments. The GRC legs are also welded structural steel with laser cut top and bottom plates for precise fit.
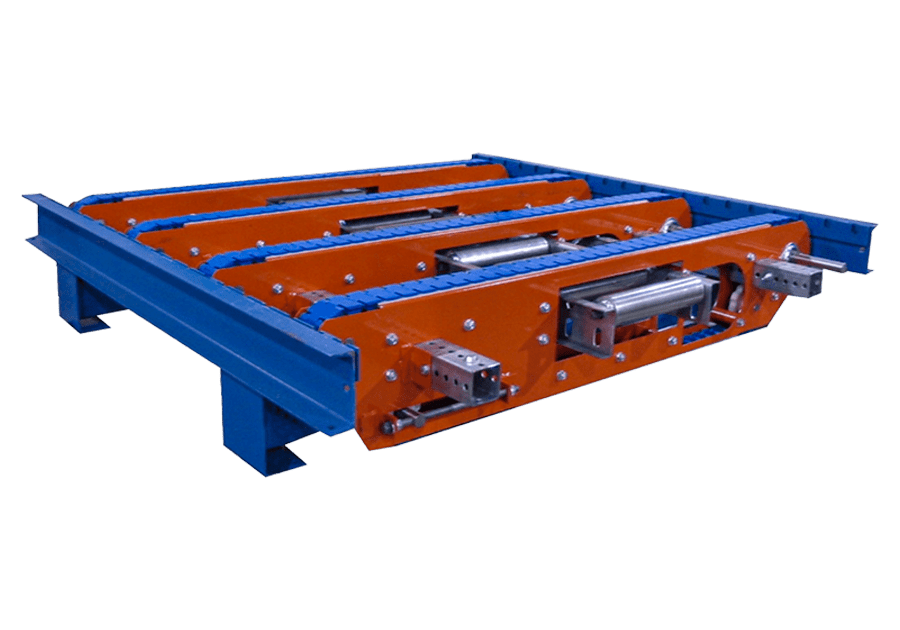
Belt Transfer Device
Systec’s Belt Transfer Device (BTD) is a safe and efficient method of moving loads onto and/or off of a conveyor line utilizing low-mark belts over chains. The features of Systec’s CTD allow it to sit within the conveyor line at various locations. It can be moved to nearly any location within the length of the conveyor line. It is totally independent of the conveyor in which it rests, and can be added to most other conveyor equipment manufacturers’ lines.
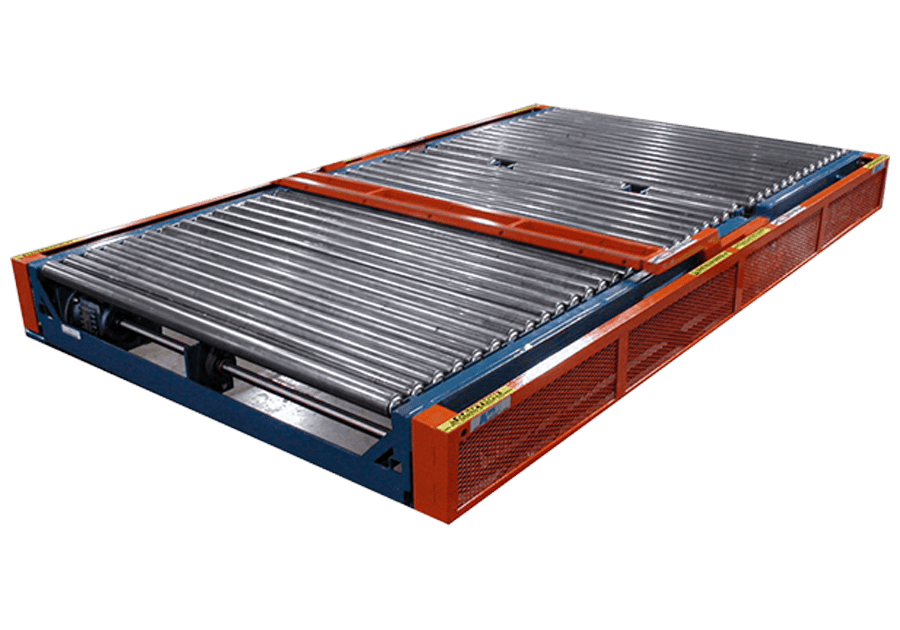
Pop-Up Infeed
Systec’s Pop-Up Infeed Device (PID) is an integral part of the conveyor line. Typically, it is used at the end of a conveyor line for transfer of a load off the line, onto a perpendicular conveyor line, or simply off the line onto a pallet, cart, or some other transport method. Systec’s Sheet Gripping Device (SGD) can be used at the end of the PID for transferring loads onto deck, or bottom dunnage sheets. The over-stroke capabilities of this device ensure the load will not only be transferred fully off the conveyor line but a full 9" beyond the end of the line. The PID can be used in Powered Accumulating Roller conveyor (PAR), Powered Roller Only conveyor (PRO), or Gravity Roller Conveyor (GRC) applications.
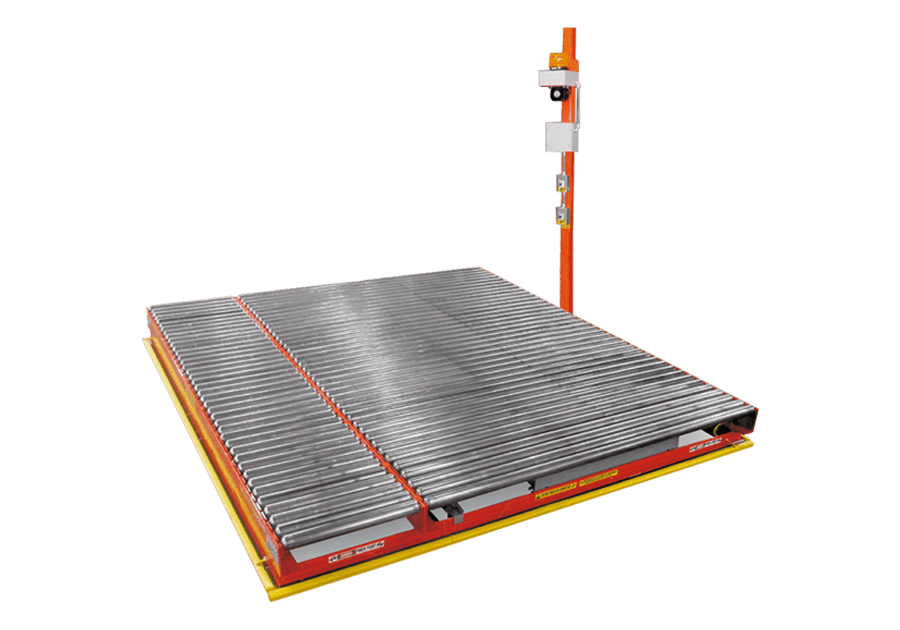
Side Pivot Conveyor
Systec’s Side Pivot Conveyor (SPC) can be used at various points within the overall conveyor system. The SPC is primarily used where change in load direction is required, yet the load orientation must remain the same. This is particularly applicable where pallets may be used within the system. This is due to the fact that the pallet’s runners, or bottom boards, must remain perpendicular to the load-carrying rollers to smoothly convey the load. The SPC is applicable at points within a conveyor line where pivoting around an obstacle, such as a building column, is required. It can also be used at a location where a break in the line may be required for equipment, such as a forklift, to gain access to an area inside the conveyor system. Each SPC is provided with a floor-mounted mast assembly with power disconnect switches and an audible and strobe-light warning system for impending conveyor movement. It also provides the necessary power for the conveyor and pivoting movement.
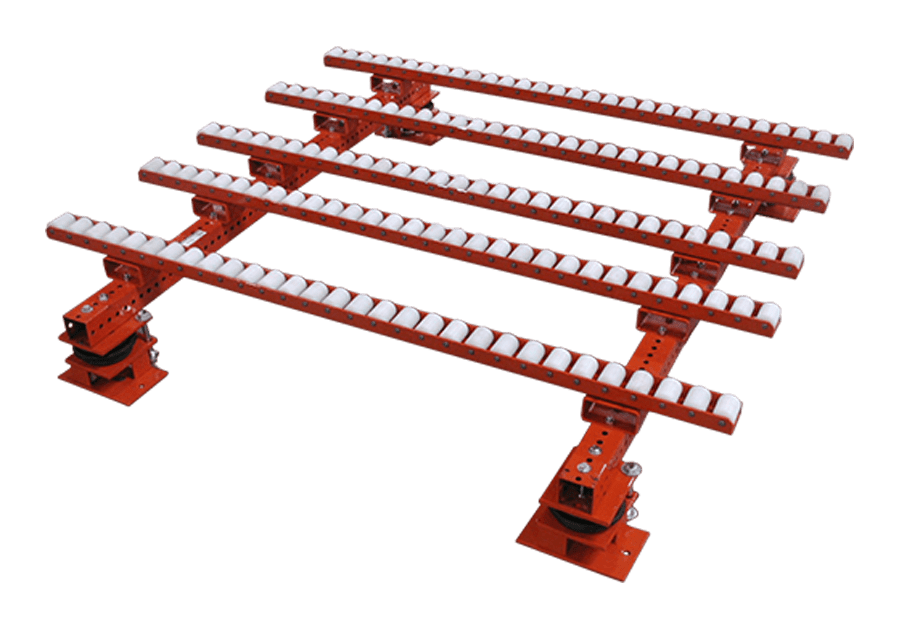
Roller Transfer Device
Systec’s Roller Transfer Device (RTD) is a very effective method of manual load movement on and/or off a conveyor line. Systec’s RTD design allows it to sit within the conveyor line at virtually any location. It can be moved, if need be, with very little effort. It is totally independent of the conveyor in which it rests, and can be added to most other conveyor equipment manufacturers’ lines. The RTD is capable of being added to a Powered Accumulating Roller conveyor (PAR), Powered Roller Only conveyor (PRO), or Gravity Roller Conveyor (GRC). Additionally, the RTD’s roller racks are fully adjustable on a 3" increment to meet any changes in load sizes or production requirements.
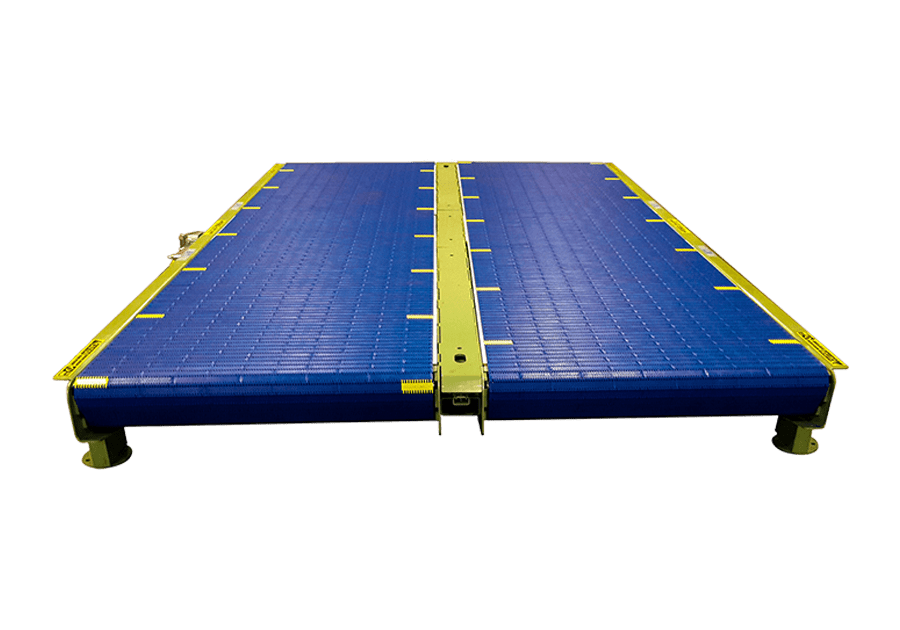
Stable Stack Conveyor
Systec’s StableStak Conveyor (SSC) is an independent conveyor line. SSC has several applications within a box plant. SSC is ideal for conveyance of loads at the corrugator discharge, where small blank handling is required. Additionally, SSC is a very suitable conveyor at a die-cut stacker for indexing loads discharged, or prior to the strapping or banding operation. At these locations, operators can walk on the conveyor’s smooth, solid surface.
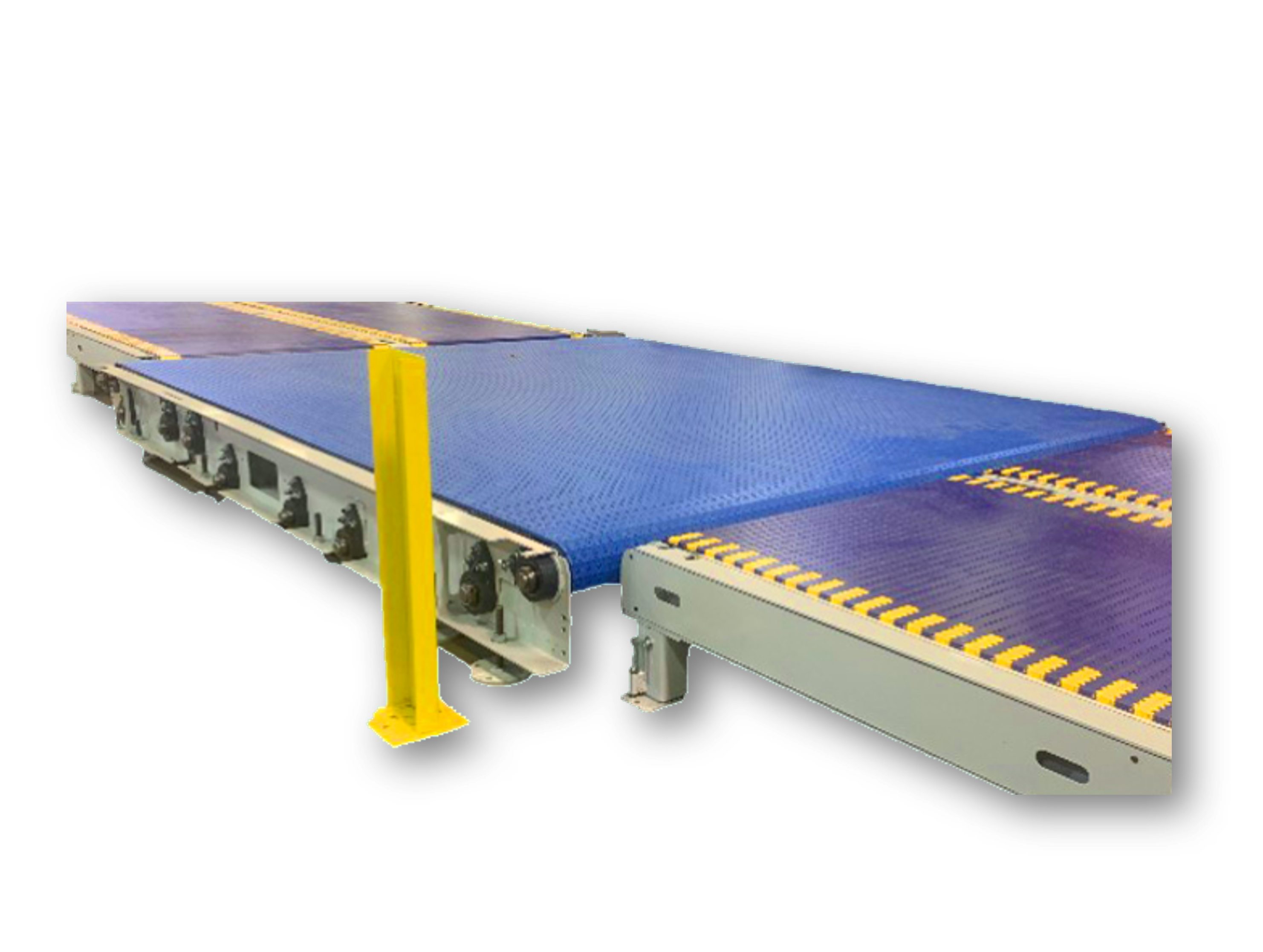
Acitve Ball Belt Rotation Device
Systec’s Active Ball Rotation Device (ABRD) utilizes the latest technology of Active Ball belt to provide a very effective method of rapid and precise load rotation. While similar in function to the Load-Rotation Device (LRD), the ABRD can rotate loads more quickly and effectively since independent devices to lift and rotate the loads are not present. The rotation feature has been maximized for efficiency and accuracy.
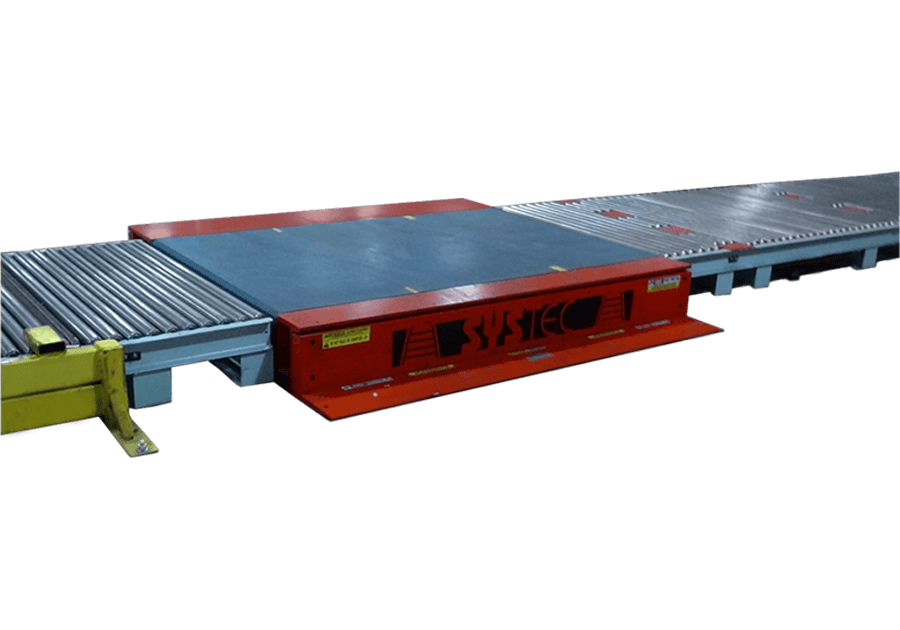
Fork Truck Crossover
Systec’s Fork Truck Crossover provides a break in the material handling system, enabling a hand truck or fork truck to pass through the line safely and effectively. The device is sized for standard fork truck and load weights while in the down (crossover) position.
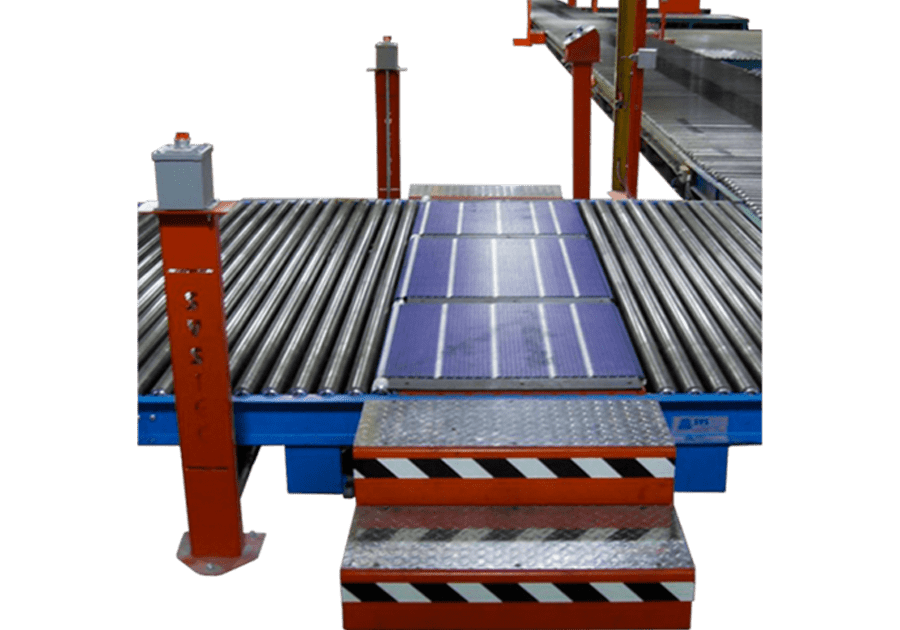
Conveyor Safe Walk (Safety)
Systec’s Conveyor Safe Walk (CSW) is a safe and efficient method of creating safe passage across any conveyor mainline. Based on the needs of the plant, the CSW can be incorporated into many different systems. Controls can be added to keep the CSW lane clear at all times, or it can be run with the push of a button. The CSW can sit within the new or existing conveyor line at various locations, and can be moved to nearly any location within the length of the conveyor line. The CSW is totally independent of the conveyor in which it rests, and can be added to all other conveyor equipment manufacturers’ lines as a stand-alone device.
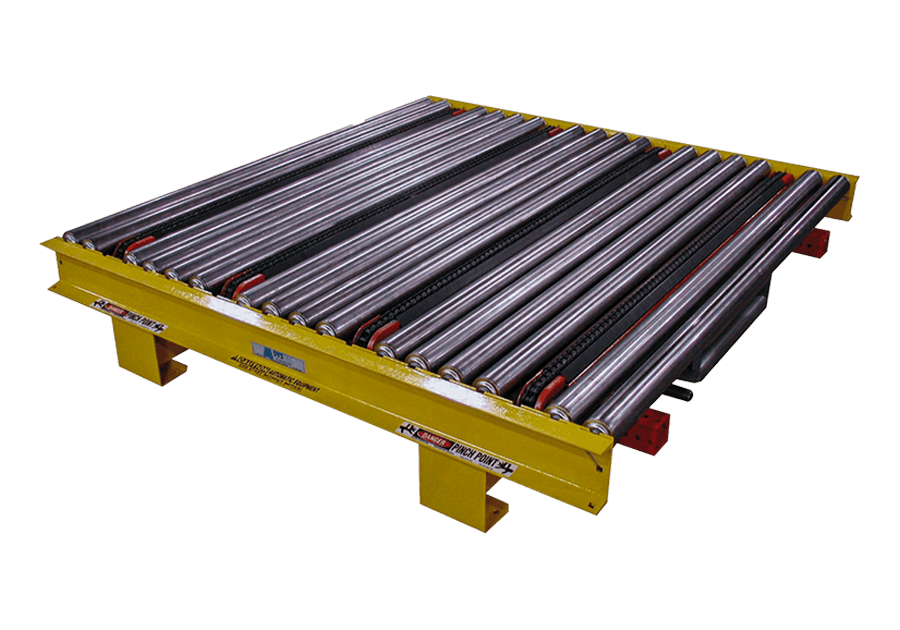
Chain Transfer Device
Systec’s Chain Transfer Device (CTD) is a safe and efficient method of moving loads onto and/or off of a conveyor line. The features of Systec’s CTD allow it to sit within the conveyor line at various locations. It can be moved to nearly any location within the length of the conveyor line. It is totally independent of the conveyor in which it rests, and can be added to most other conveyor equipment manufacturers’ lines. The CTD is capable of being added to either a Powered Accumulating Roller conveyor (PAR), Powered Roller Only conveyor (PRO), or Gravity Roller Conveyor (GRC). The device can act as a one-, two-, three-, or four-way intersection.
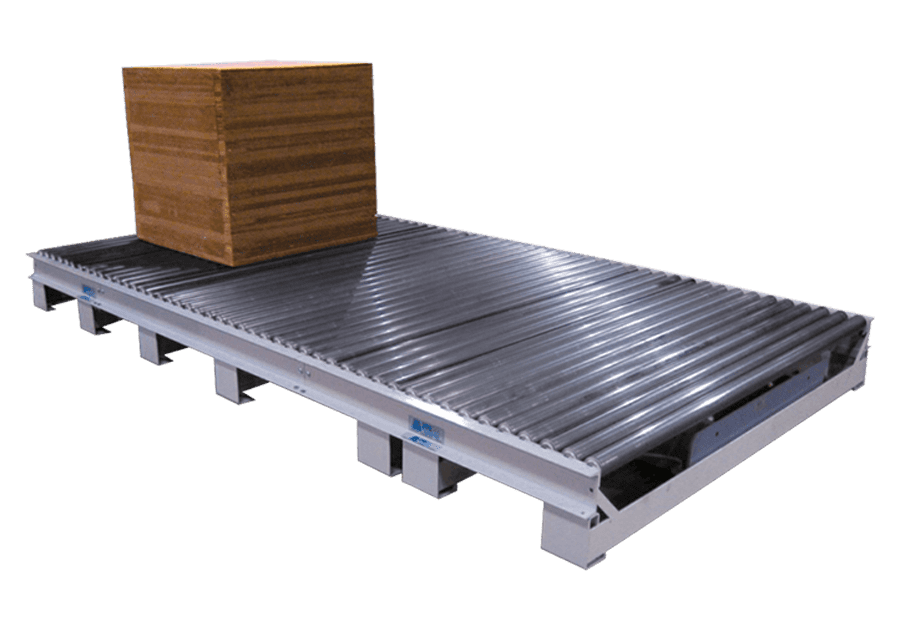
Powered Roller Conveyor
Systec’s Powered Roller Conveyor is provided as a powered accumulating roller (PAR) or a powered roller only (PRO) conveyor. The features of the PAR conveyor are the fully accumulating drive, take-up, and intermediate sections, or midsections. PAR conveyor allows loads to be added to a conveyor line without disruption or movement of loads already present on the line. With optional control features, loads can be added to the conveyor line until it is full, maximizing utilization of the entire conveyor line. Another control option would be multiple areas of accumulation, or zones, for loads to move independently and stage down the conveyor line. The accumulation features of PAR conveyor allow a single, one-horsepower drive to run up to 70' of conveyor. Systec’s PRO conveyor features a positive drive on the entire conveyor line and allows loads to be “indexed” as each load is added to the conveyor line.
High-Speed Transfer
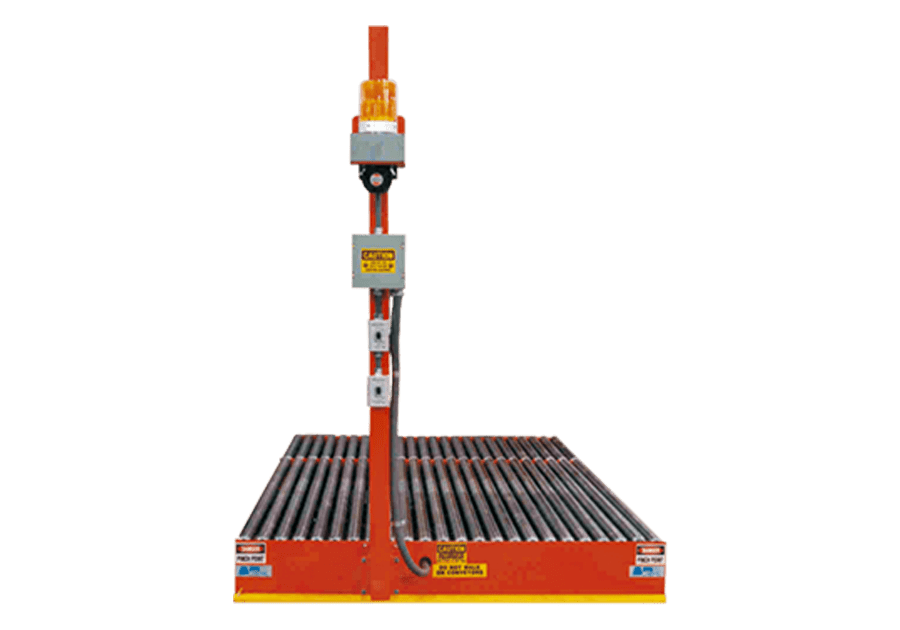
Shuttle Automatic Car
Systec’s Shuttle Automatic Car (SAC) can be used at various points within the overall conveyor system. The SAC is primarily used where a break in the conveyor line is required, or a single line may need to deliver to more than one location. It can also be used at the infeed of converting equipment to allow machine opening without interference.
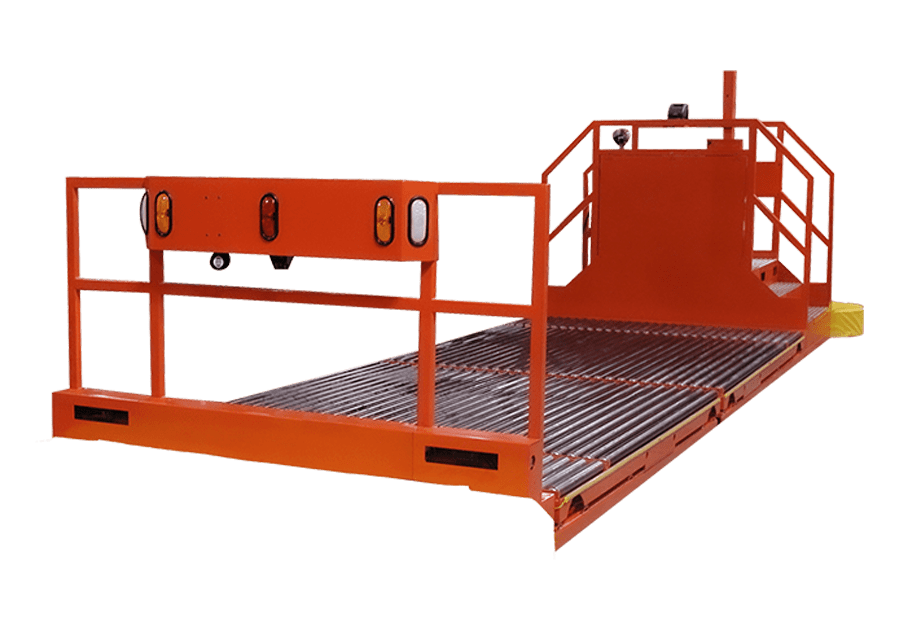
Transfer Car
The Systec Manual/Automatic Transfer Car has several unique features providing superior performance. The Transfer Car brings an abundance of safety features such as laser pathway sensors, audible and visual alert system and available operator visual assistance system. The two-piece design allows the car to “follow” floor contours during movement, although floor flatness is critical to long-term car performance. All wheels feature Ringfeder locking hubs for ease of maintenance. Safety features include laser object detection with automatic slowdown and stop for objects or personnel in the car path, warning lights, and strobe lights that alert personnel to car movement. Systec also has a high-speed car variation that is able to move at high speeds in secured (gated) pathways.
Load Rotation / Repositioning
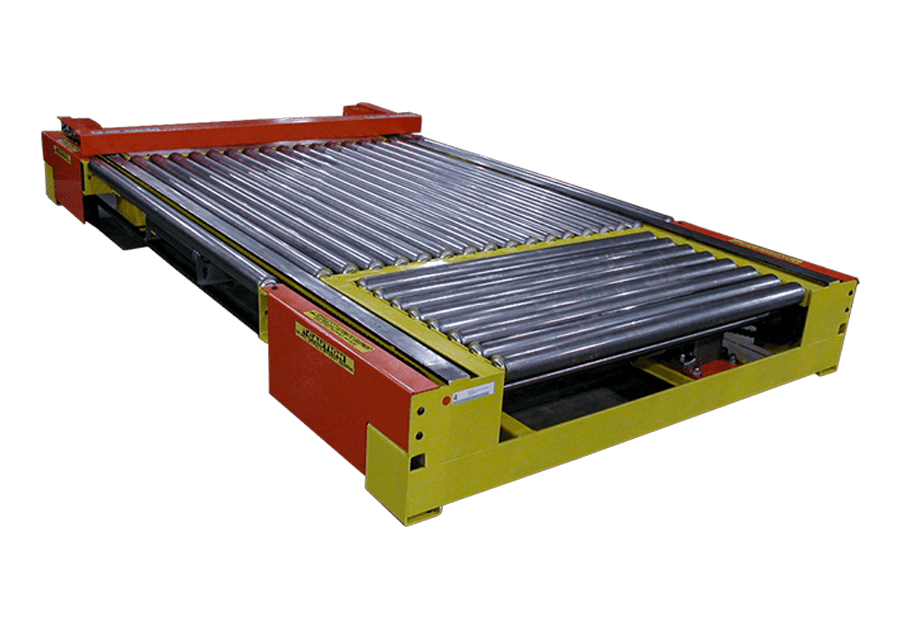
Pusher Transfer Device
Systec’s Pusher Transfer Device (PTD) is an integral section of the conveyor line. The device can be equipped with a conveyor drive section, take-up section, or midsections, or can be gravity. The PTD can be set in the line to that will push either right, left, or both directions.
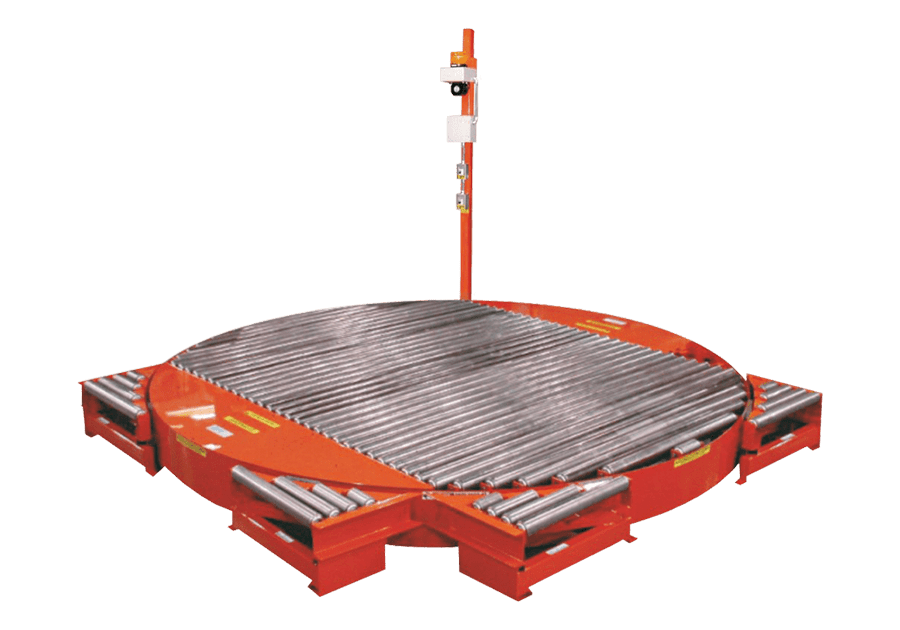
Center Pivot Conveyor
Systec’s Center Pivot Conveyor (CPC) can be used at any point within the overall conveyor system. The CPC is primarily used where change in load direction is required, yet the load orientation must remain the same. This is particularly applicable where pallets may be used within the system.
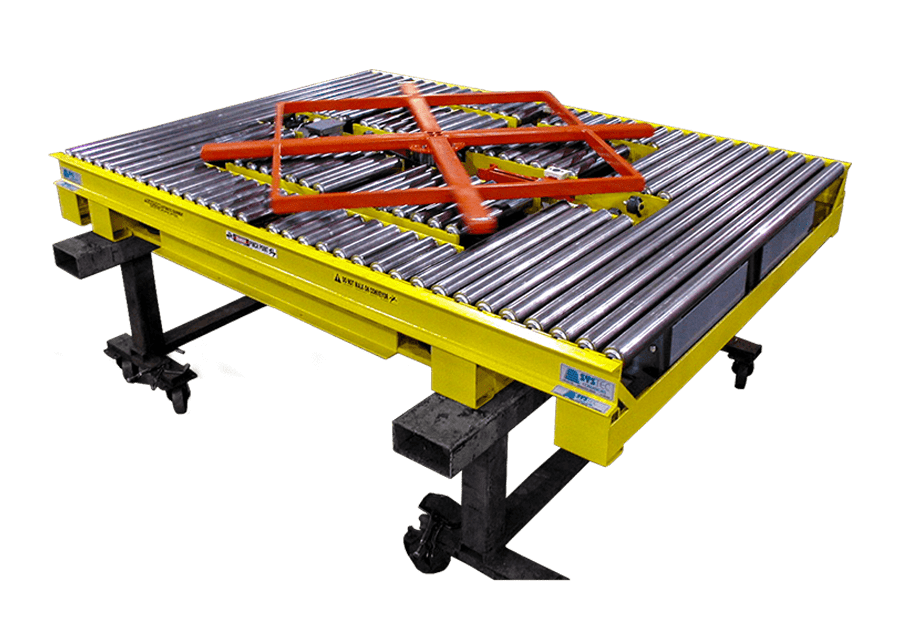
Load Rotation Device
Systec’s Load Rotation Device (LRD) is a very effective method for automatically rotating loads in 90-degree increments. As with all Systec conveyor and devices, the LRD is an all-welded steel construction, using precision laser-cut parts for exact fit and function. This is a very low-maintenance device, applying the most advanced safety designs and features. It is extremely friendly with pallets as well.

Load Centering Device
Systec’s Load Centering Device (LCD) is a very effective method for automatic load centering.
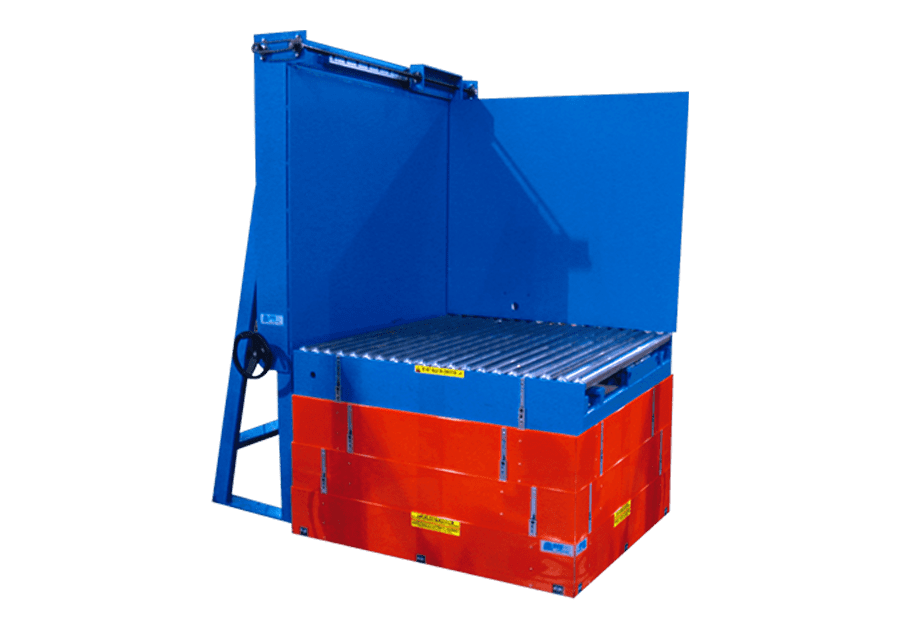
Unit Load Downstacker
Systec’s Unit Load Downstacker (ULD) is an ergonomic solution for manual load forming stations. This is a very low-maintenance device applying the most advanced safety designs and features, including a conveyor lift table and adjustable backstop system. The conveyor table can be elevated to a comfortable work height, allowing the operator to transfer bundles of boxes from the bundle conveyor to the ULD station without bending. As each tier is completed, the operator can activate the lift, lowering it to a comfortable work height, to add the next tier of bundles to the unit load. As the lift is actuated for movement, the stationary and adjustable backstops retract for load clearance. Once the lift has been stopped, the backstops return to the original position for continuation of load building. The ULD adjustable backstop can be adjusted to position the unit load as required, and minimize the effort.
Support Services
Technical Support Services
Find the latest upgrades and improvements available for your Inspire Automation equipment.
- Remote Technical Support: M-Guard and AutoView Remote Monitoring Systems
- Inspire Advantage Program: Long-Term (Annual) Service/PM Program
- Service Audit Programs
- After-Hours Service Support
- Remote Service Technology
Product Support Services
Get support relating to the specific products currently being used in your operation.
- Spare Parts Packages
- Dedicated Spare Parts Fulfillment Center
- Support for Other OEM Products
Product Features and Benefits
Our product features enable you to maximize the operation and efficiency of your equipment.
- Fewer Direct Connect drives
- ASI Framework—Less Wiring
- Less Hardware with Welded Frames
- Fewer Bearings, Sprockets, and Chains
- Fixed, Laser-cut, Pressure Racks with No-Stop Bolts
- Maintenance-free Gear Motors
- Lifetime Lubricated Bearings
Technical Support Services
Product Support Services
Product Features and Benefits
Get in touch
Interested in Our Material Handling Automation Solutions?
Want to know more about Material Handling Automation? Or maybe you’re looking for service, ordering replacement parts, or need a quote on a product? We’re here to help.
Send Request