Troubleshooting Common Conveyor Problems
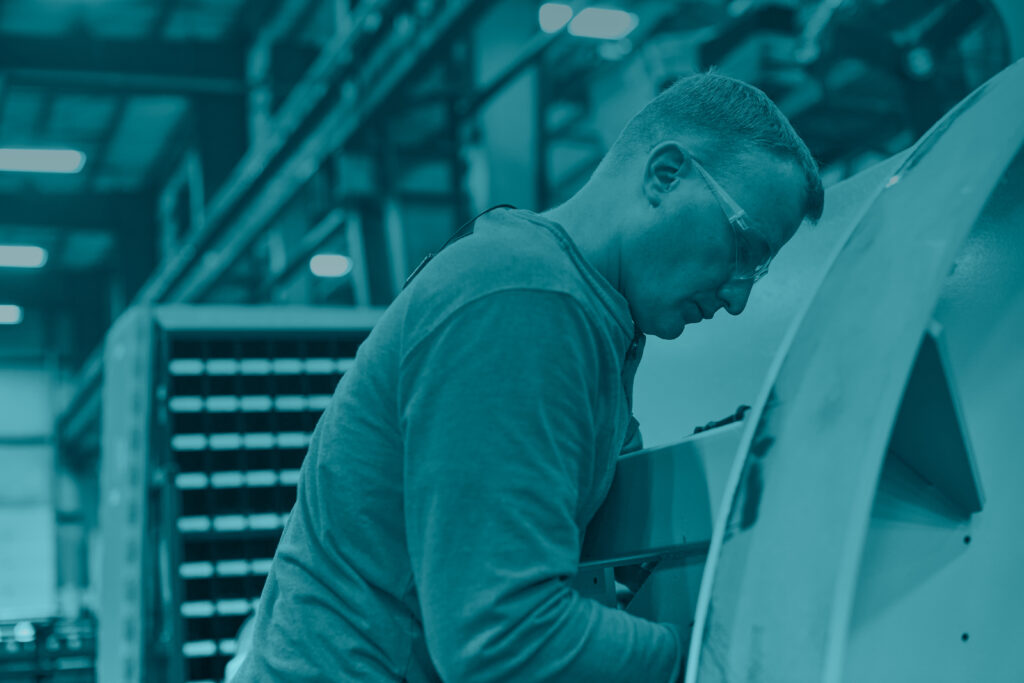
Introduction
Conveyors are indispensable in various industries, ensuring efficient material handling and production processes. However, like any mechanical system, they are prone to issues that can halt production and lead to costly downtime. This blog aims to explore common conveyor belt problems, emphasize safety protocols, and outline a preventive maintenance program to keep your conveyor systems running smoothly.
Common Conveyor Problems and Their Impact
Conveyors are critical, and their downtime can result in substantial revenue loss. Identifying and addressing common problems can minimize disruptions and extend the life of your equipment.
Belt Misalignment
Misaligned belts on Stable Stack conveyors cause uneven wear, damage conveyor components, and can lead to potential hazards. Regularly checking and adjusting alignment ensures smoother operation and prolonged belt life.
Slippage
Belt slippage reduces efficiency and can damage the belt. Common causes include improper tension, worn pulleys, and excess moisture. Tackling slippage involves regular belt tension checks and ensuring pulleys are in good condition.
Debris and Corrugated Dust
Debris and corrugated dust in the corrugated manufacturing process can cause slip hazards and excessive wear on mechanical components. Regular cleaning and proper load management can mitigate this issue.
Photo-Eye Alignment/Replacement
PLC programs do not “change themselves.” Nearly all of the time it is reported that a device is no longer behaving as it was programmed, we find that PE alignment is a contributing root cause. Verification that a PE is properly triggered when blocked via the indicator light is a quick method to confirm alignment. When the indicator isn’t highlighting this event, it is usually either PE misalignment or a bad PE that needs to be replaced.
Motor and Gear Issues
Motor and gear failures halt conveyor operations for both roller and Stable Stack conveyors. Causes include lack of lubrication, worn-out parts, and electrical issues. Regular maintenance and timely repairs are crucial to avoid such failures.
Emphasizing Safety
Safety is paramount in any industrial setting, particularly with conveyor systems. Implementing and adhering to safety protocols protect personnel and equipment. Consider a production facility where a conveyor system malfunction led to an emergency. Having adequate quantities and spacing of walk-plates for roller conveyor, and the inclusion of the Systec Conveyor Safe Walk are two key items to aid in safe employee crossing of conveyor systems.
Safety Labels and Guards
Always ensure safety labels and guards are in place to warn personnel and prevent accidents. Labels should be legible and guards securely installed to protect against moving parts.
Emergency Routes
Establish and clearly mark emergency routes throughout the facility. Employees should be aware of these routes to ensure a quick and safe evacuation in case of emergencies.
Preventive Maintenance Program
A robust preventive maintenance program minimizes unplanned downtime and extends equipment life. Here’s how to structure an effective maintenance schedule.
Routine Checks and Maintenance Schedule
Develop a schedule for routine checks of belt tension, alignment, and overall condition. Regular inspections help identify and address minor issues before they escalate.
Lubrication
Proper lubrication of gear motors and bearings reduces wear and prevents breakdowns. Schedule regular lubrication to ensure smooth operation.
Cleaning and Housekeeping
Keep the conveyor system clean to prevent material buildup, which can cause slippage and spillage. Implement a regular cleaning schedule as part of maintenance. Thoroughly clean dust and debris from beneath conveyors. Debris or pieces of board that have been shoved beneath the conveyor can cause significant issues. Strapping around drives makes the motor work harder and possibly become hot. Dust beneath the conveyor may begin to smolder from the extra heat generated from the motor. Schedule regular cleanings, and don’t forget to dust off the photo electrics after cleaning.
Energy Conservation Controls
Your conveyor system should also stop during long pauses in production. Energy conservation controls power down to zero-state after lack of activity, resulting in lower energy costs and extended conveyor life.
Backup Copies and System Checks
Maintain backup copies of PLC programs, schematics, and layouts. This ensures quick recovery in case of power surges or system failures. Perform regular system checks to verify backups are current and accurate.
Conclusion
Maintaining your conveyor system involves identifying common issues, emphasizing safety, and implementing a preventive maintenance program. These steps ensure smooth operations and protect both your equipment and personnel. Stay proactive and diligent to maximize the productivity and lifespan of your conveyor belts. By prioritizing regular maintenance checks, adhering to safety protocols, and being prepared for emergencies, you can mitigate risks and ensure the continuous and efficient functioning of your conveyor systems.
Contact Inspire Automation
For expert advice and assistance with your conveyor system, contact Inspire Automation. Our team of professionals is ready to help optimize your system’s efficiency and longevity.
More from the Blog
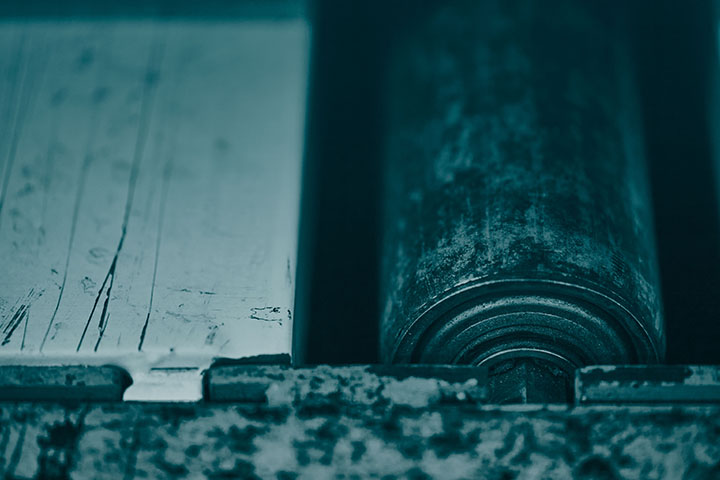
Embracing Industry 4.0: IoT, Big Data, and the Evolution in Conveyor Automation
Discover how Industry 4.0, IoT, and Big Data redefine conveyor automation, enhancing efficiency and optimizing the manufacturing process.
Read Full Article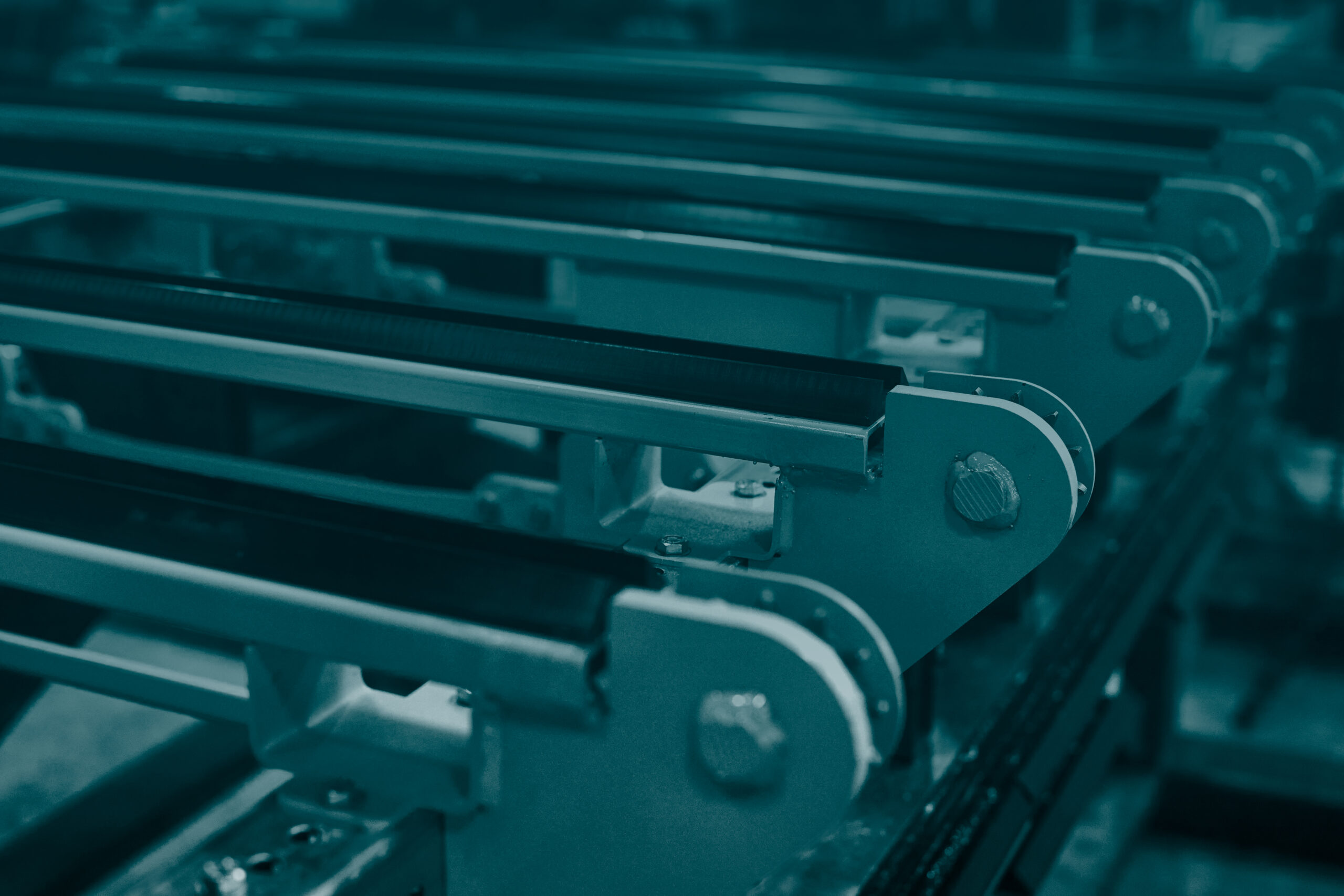
Maximizing Your Machinery Investment: Key Strategies for Long-Term Success
Investing in machinery is a significant decision, but getting the most out of it requires more than just purchasing the best equipment. It’s about building a long-term partnership with a supplier who is as committed to your success as you are.
Read Full Article