Sensor Maintenance Tips and Recommendations
Many of the complex solutions here at Inspire Automation rely on a variety of components in order to function. Today we’re highlighting one of the most crucial elements of any quality robotics or automation system – sensors.
Specifically, we’re discussing the importance and specifics of sensor maintenance. We at Inspire Automation know how vital servicing these components is. Doing so will keep robotics and automation solutions working reliably, allowing users to get all of the functionality out of these devices that is intended.
It’s interesting to think that such a small piece of a setup can have such a profound impact on performance, but it can. This is because the sensors play a large role in automating the activities of a system, triggering appropriate responses, and helping various components communicate with one another.
Proactive sensor maintenance, cleaning, and troubleshooting can be hugely valuable for any organization. Let’s start by examining what these components do, and understanding the essential role they play in robotics and automation solutions.
What Are Sensors? What Function Do They Have in Equipment?
In the realm of modern manufacturing, the integration of cutting-edge technologies has ushered in an era of efficiency and precision. At the heart of this transformation lie sensors, crucial components that play a pivotal role in the seamless operation of robotics and automation systems.
Sensors are devices designed to detect and measure physical properties, converting real-world information into electrical signals. In the context of our equipment, sensors act as the eyes of our automated systems, capturing crucial data load proximity and measurement data for our automation systems to make informed decisions in real-time. They bridge the gap between the physical and digital worlds.
One of the primary functions of sensors in our systems is to monitor and control promixity, speed, and physical dimensions.
These data points are essential for ensuring optimal performance, quality control, and adherence to safety standards.
Sensors Are a Source for Continuous Improvement
Sensors enable automated machines to adapt to dynamic conditions, adjusting their operations based on real-time feedback. This adaptability is crucial in scenarios where manufacturing processes require constant optimization for maximum output and resource utilization.
Sensors serve as the linchpin in the world of manufacturing solutions, providing the critical data needed for robotics and automation systems to operate seamlessly. Their ability to capture, process, and respond to real-world information not only ensures precision and efficiency but also paves the way for the continued evolution of smart and connected manufacturing ecosystems.
But all of these amazing benefits and ROI-enabling perks are only possible under one condition. Companies must follow the best practices for sensor care, which includes proactive sensor maintenance, proper sensor cleaning techniques, and correctly troubleshooting sensor issues.
Tips for Sensor Maintenance: Maintaining and Optimizing Your Valuable Equipment
Effective sensor maintenance is vital to ensure the optimal performance and longevity of these critical components in various systems. The process begins with a thorough examination of the sensors themselves. Technicians need to inspect for physical damage, wear, or any signs of corrosion. Regular visual checks help identify potential issues early on, preventing costly downtime in manufacturing processes.
Ideally, sensors should be checked before installation and thoroughly tested according to device-specific standards. Depending on who installed your sensors or how old they are, they may need to be tested, calibrated, or otherwise modified to ensure smooth performance.
But of course, we know that sensors don’t function alone. Their true value shines in their connection to other components – which means these components must also be considered when it comes to maintenance procedures.
The Importance of Equipment Inspection and Calibration
Once the sensors are inspected, attention turns to the machine components they control. Proper greasing of moving parts is crucial to prevent friction-related wear and tear. Lubrication not only extends the life of the machinery but also ensures that sensors can accurately capture and interpret data. Regular greasing schedules, based on manufacturer recommendations, are essential to maintain smooth operation.
Calibrating sensors is equally important. Accurate sensor readings are imperative for precision in manufacturing processes. Calibrating sensors ensures that they provide reliable and consistent data. This process aligns the sensor’s output with the actual conditions it is monitoring, enhancing the overall accuracy of the system.
Observing equipment in motion is the final step in sensor maintenance. This involves monitoring the sensors while the machinery is operational to ensure seamless activity. Any irregularities, deviations, or unexpected behavior can be identified during this phase. Regular observation allows for the prompt detection of potential malfunctions or deviations from the norm, enabling proactive maintenance before issues escalate.
In essence, a comprehensive approach to sensor maintenance involves examining the sensors themselves, greasing and calibrating the machine components they control, and observing equipment in motion. This proactive strategy not only extends the lifespan of sensors but also contributes to the overall reliability and efficiency of manufacturing systems.
Sensor Cleaning: A Thorough Approach for All Connected Components
Ensuring the proper functionality of sensors and light curtains is paramount in maintaining the efficiency of manufacturing systems.
Regular cleaning of these components is a fundamental aspect of sensor maintenance. Dust, debris, or contaminants can compromise their accuracy and responsiveness. Using a soft, lint-free cloth and, if necessary, a mild cleaning solution helps remove any buildup without causing damage. When in doubt, contact the manufacturer about specific recommendations for cleaning techniques.
Moving beyond sensors, attention should be directed towards the robot arms and their base. Over time, these surfaces can see the buildup of:
- Grime
- Lubricant residue
- Dust
- Machine scraps
- Corrosion
These contaminants can potentially affect the range of motion and precision of the robotic system. Thoroughly cleaning these components not only enhances the aesthetic appearance but also contributes to the overall operational effectiveness.
Cleaning agents compatible with the materials used in the robot construction should be employed to prevent any adverse reactions.
Additional Areas to Consider During the Cleaning Process
To complete a comprehensive cleaning routine, focus should extend to the ventilation system. Vents, fans, and filters play a critical role in regulating the temperature of the machinery.
Accumulation of dust and debris can impede airflow, leading to overheating and decreased performance. This can sometimes make it seem like a sensor isn’t reading properly, even if it isn’t the component experiencing problems. Regularly cleaning these components ensures optimal heat dissipation and helps prevent potential malfunctions.
A meticulous cleaning regimen is essential for maintaining the functionality of sensors and light curtains, cleaning robot arms and bases from grime and lubricant residue, and ensuring the cleanliness of vents, fans, and filters. This holistic approach not only preserves the aesthetic appeal of the equipment but also safeguards against potential issues that may arise from neglecting the cleanliness of critical manufacturing components.
What Else Should Be Checked to Optimize Sensor Performance?
Beyond the direct inspection of sensors, a comprehensive maintenance routine involves evaluating various aspects of the machine to optimize sensor performance. Here are some of the important tasks to consider when servicing your sensors and their equipment.
Fluid Levels: Hydraulic and lubrication fluids play a crucial role in the smooth operation of machinery. Regular checks ensure that fluid levels are within the specified range, preventing issues such as overheating and component wear that might affect sensor performance.
Battery Performance: Battery performance is another key consideration. Many automated systems rely on batteries to power sensors and control units. Regular inspections of battery health, including voltage levels and overall condition, are essential to prevent unexpected failures and ensure continuous and reliable sensor operation.
Check Seals: Proper sealing is paramount for maintaining the integrity of the machine. Hoses, connection points, and seals should be inspected for any signs of wear, damage, or leakage. A well-sealed system prevents the ingress of contaminants that could interfere with sensor accuracy and responsiveness.
Tighten Connections: Tight connections play a crucial role in overall machine stability. Bolts, nuts, and screws should be inspected regularly to ensure they are securely fastened. Vibrations and constant movement in a manufacturing environment can lead to loosening over time, potentially affecting the alignment and positioning of sensors. Tightening connections as part of routine maintenance helps prevent issues related to sensor misalignment and ensures the overall stability of the machine.
In summary, a thorough inspection of fluid levels, battery performance, proper sealing, and tight connections is essential for creating an environment that allows sensors to perform optimally. This holistic approach to machine maintenance not only enhances sensor reliability but also contributes to the overall longevity and efficiency of the entire automated system.
Benefits of Proper Sensor Care, Maintenance, and Cleaning
Proper care, maintenance, and cleaning of sensors in manufacturing environments yield a multitude of benefits, ranging from better performance to enhanced safety and operational efficiency. One of the primary advantages is cost savings.
Regular maintenance and cleaning prevent unexpected breakdowns and extend the lifespan of sensors and associated machinery. By addressing issues proactively, companies reduce the need for costly emergency repairs and replacements, ultimately saving on both repair expenses and potential production losses during downtime.
Less downtime is another significant advantage. Well-maintained sensors contribute to increased equipment reliability, minimizing the chances of unexpected failures that can lead to production stoppages. This reduction in downtime translates to higher overall productivity and output, positively impacting the bottom line.
Ensuring the longevity of equipment is a key outcome of proper sensor care. Regular cleaning, lubrication, and inspections contribute to the sustained functionality of sensors and the machinery they control. This extends the lifespan of the entire system, delaying the need for expensive upgrades or replacements and providing a better return on investment over time.
Proper sensor care also contributes to safe performance. Sensors play a crucial role in monitoring and controlling various parameters, ensuring that machinery operates within specified limits. Regular maintenance helps prevent malfunctions that could compromise safety, protecting both personnel and equipment from potential accidents.
Just as sensors are far more than the tiny components they appear to be, the benefits of proper sensor care, maintenance, and cleaning extend far beyond just the sensors themselves. They include cost savings, reduced downtime, extended equipment longevity, and enhanced safety – all of which contribute to a more efficient, reliable, and cost-effective manufacturing operation.
Inspire Automation is Here to Serve You
How can you ensure the proper functionality of your equipment, including the sensors? It involves knowing and implementing the best practices for sensor care. Proactive sensor maintenance, along with maintenance of the associated components, will keep your equipment working properly.
You can make these processes much easier by working with the right partner. Inspire Automation is not only a provider of world-class robotics and automation solutions, but we also pride ourselves on our amazing support. This includes:
- Technical support with remote monitoring and servicing, service audit programs, and after-hours support
- Product support including spare parts packages from our dedicated fulfillment center, plus support for other OEM products
- Product features and benefits including ASI framework, maintenance-free gearmotors, lifetime lubricated bearings, and much more
Are you looking for high-quality equipment, where all components including sensors are designed to exceed expectations? Better yet, do you want a supportive company providing these systems, along with service to ensure you’re completely satisfied? If so, contact Inspire Automation today.
More from the Blog
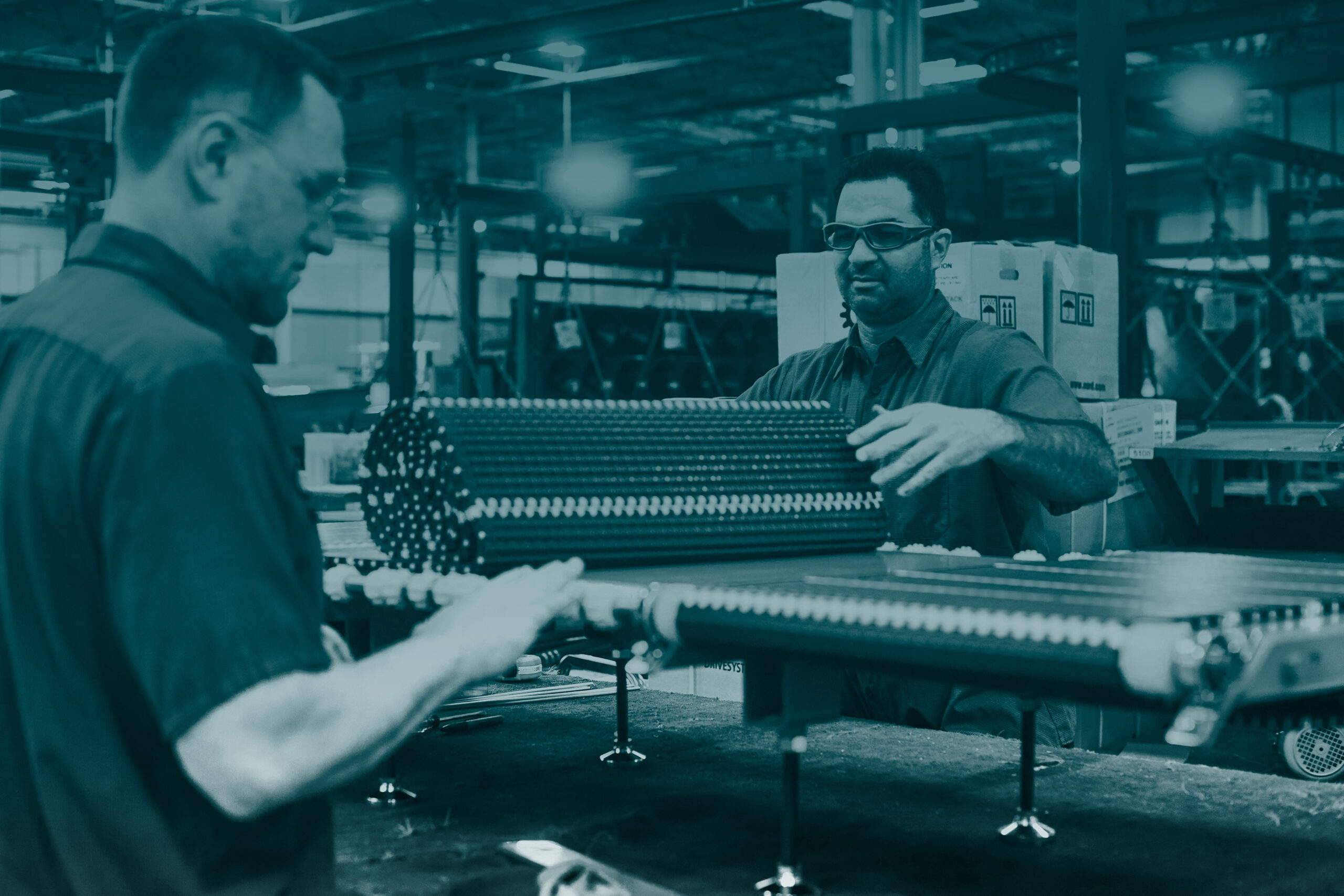
Extended Service Agreements: Your Safety Net for Uninterrupted Performance
Long-term service and support agreements can be the guardrails for success in your industry. With Inspire Automation, these agreements are part of a commitment to our clients—a pledge to deliver uninterrupted service and steadfast support.
Read Full Article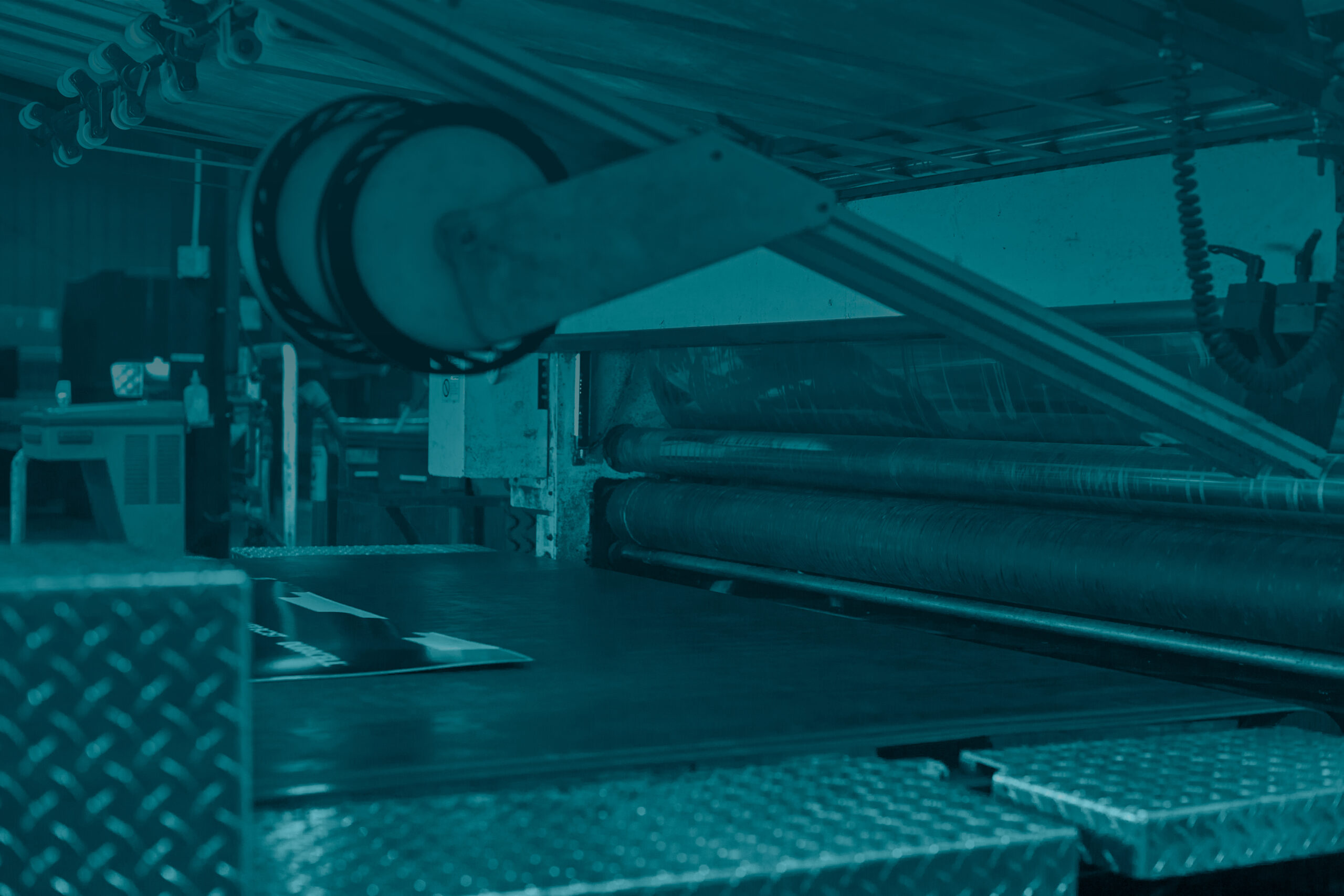
Advantages of Litho Labeling and Why It’s Still Relevant
In the dynamic landscape of packaging, litho labeling continues to stand out as a reliable and advantageous choice for high quality labeling requirements in corrugated production, and one of the top solutions at Inspire Automation.
Read Full Article